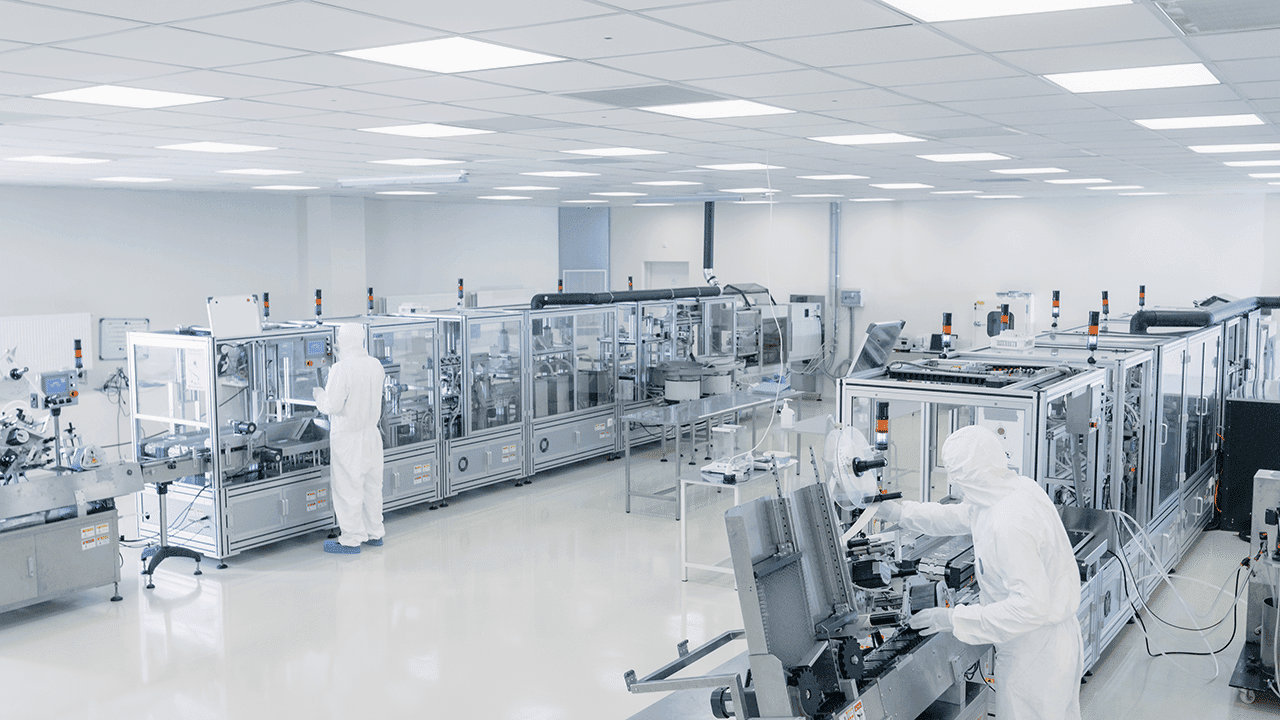
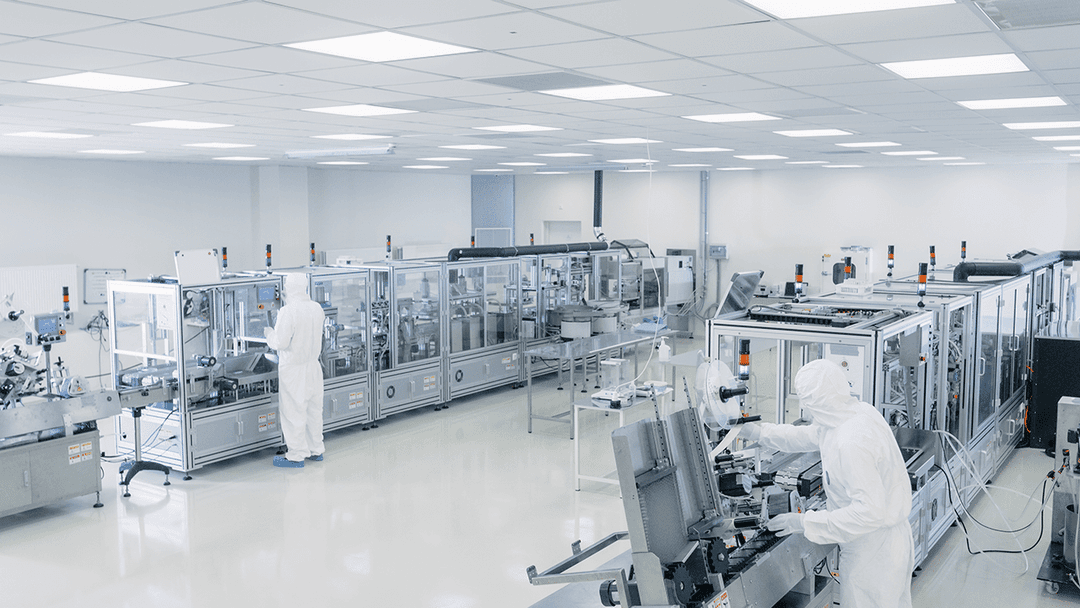
ISO 6: Defining Cleanroom Classification Guidelines
ISO 6: Defining Cleanroom Classification Guidelines
What Is A Cleanroom? The old American cleanroom standard; FS 209E Clause 3.5 Defined a cleanroom as 'A room in which the concentration of airborne particles is controlled and which contains one or more clean zones. ' FED-STD-209E was discontinued in 2001 and superseded by the ISO standard but we still hear reference to class 100/1,000…
What Is A Cleanroom?
The old American cleanroom standard; FS 209E Clause 3.5 Defined a cleanroom as ‘A room in which the concentration of airborne particles is controlled and which contains one or more clean zones. ‘
FED-STD-209E was discontinued in 2001 and superseded by the ISO standard but we still hear reference to class 100/1,000 etc which mirror the ISO 14644 standard.
There are 9 ISO classifications, ISO 1, ISO 2, ISO 3, ISO 4, ISO 5, ISO 6, ISO 7, ISO 8, and ISO 9. ISO 1 is considered the cleanest while ISO 9 is considered the dirtiest. The basis of cleanroom standards is the number of particle per m3 of air.
Table 1 from ISO4644-1:2015 illustrates the maximum concentration limits in each class.
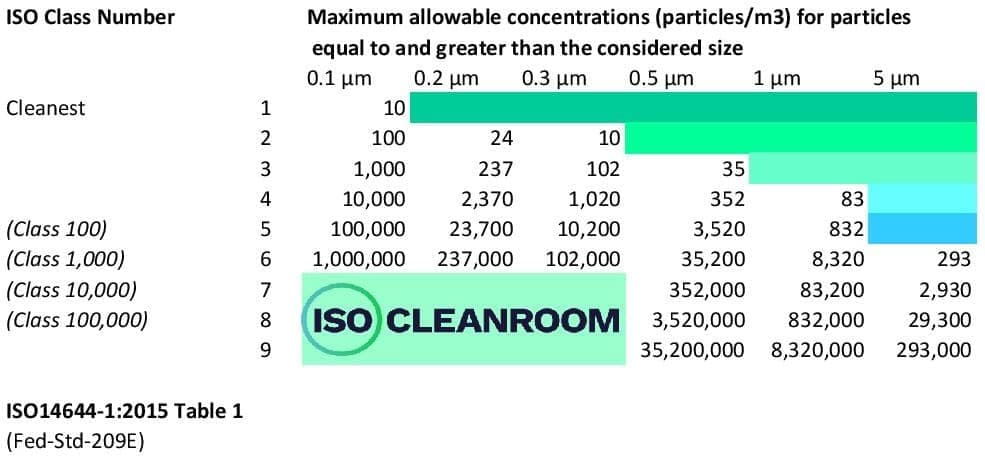
What is an ISO 6 Cleanroom?
An ISO 6 cleanroom are required to contain a maximum of 35,200 particles >0.5 micron per cubic meter and 293 particles at >5 micron.
Before choosing an ISO classification it is vital to firstly determine what size and number of particles can negatively affect your materials or process.
Why Do You Need an ISO 6 Cleanroom?
An ISO 6 cleanroom is required to control the environmental variables making production or the results when performing a particular process safer and or more reliable.
Those in life science industries tend to be concerned with the safety that a cleanroom can provide where as technology lead industries are more concerned with the increase in yield that a cleanroom will provide.
How To Get an ISO 6 Cleanroom?
In order to achieve the required particulate levels to be classified as an ISO 6 Classroom the cleanroom needs to be heavily controlled. The cleanroom design must consider;
The air entering the cleanroom should filter the particulate that have been determined as detrimental to the process to be carried out in the space. This will use a series of graded filters.
It must have sufficient airflow to dilute any particulate present. An ISO 6 Cleanroom should have in excess of 150 complete air changes per hour. The amount of air changes in the room will deteriorate as the filters block and so it is important to design to a specific time frame.
The airflow must be designed to carry any particulate to an exit. The air must move from the clean more sensitive parts of the process to the less sensitive.
In order to control the amount of particulate that enters the cleanroom on operators and materials, airlocks are required.
A risk assessment of the process to take place within the cleanroom should be undertaken and from these findings a robust set of SOP (standard operating procedures) implemented.
How to Maintain an ISO 6 Cleanroom?
The SOP will cover all aspects of maintaining the ISO 6 Cleanroom. The SOP will usually cover the following but every industry and process will have additional specifics to consider.
- Check for constant positive pressure
- Regular checks to the particle level within the room
- All Personnel wearing the specified PPE
- Regular validation to check the air filtration and dilution (Air flow)
- Regular and extensive cleaning procedure
- Material selection criteria for any items going into the cleanroom
- Control who can enter the cleanroom and ensure adequate operator training prior to entry
Are you looking for a cleanroom? Contact us now to know more!