Cleanroom Design
Cleanroom Design
As part of our cleanroom design and build package we provide full working drawings, design calculations, guidelines and product specifications of the materials selected to meet your brief.
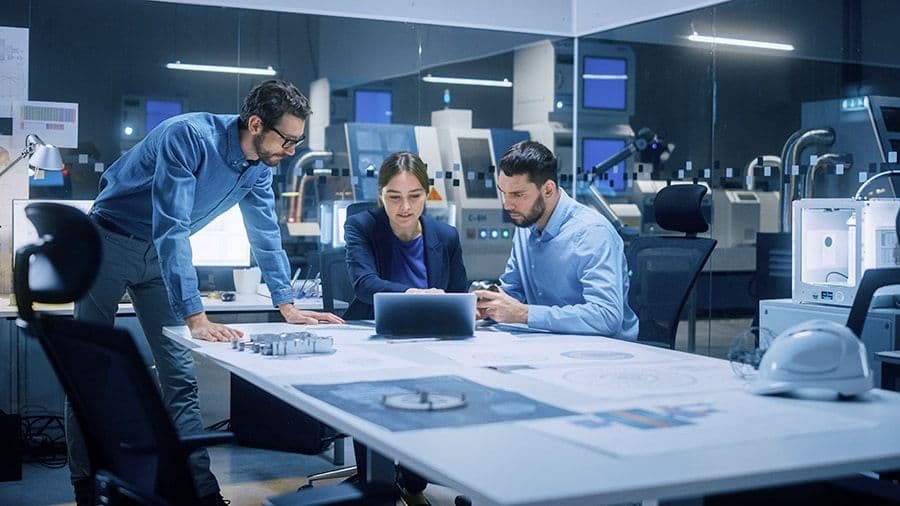
Cleanroom design specification
Specifying the classification of your cleanroom
Many industries are required to perform at least one of their processes within a controlled environment. The internationally recognised specification system for these spaces is defined by the ISO (The International Organisation of Standards) and it is the first question that needs answering before any cleanroom design can commence. Your client, government organisation or regulatory board will refer to this ISO 14644-1:2015 standard when detailing the minimum air cleanliness levels they require of your production, storage or assembly space.
There are processes, especially in the research and development arena where the minimum required ISO 14644 classification is not defined and the task of agreeing on the appropriate level can prove more difficult. ISO have compiled the table below to help specifiers select a suitable ISO classification level.
Application | Classification (ISO class) | |
Advanced Engineering | Aerospace | 5 to 7 |
Composite materials | 8 | |
General background | 8 | |
Isolation of Injection Moulded Parts | 7 to 8 | |
Optical | 7 to 8 | |
Touch screen assembly | 7 | |
Consumables | E-Liquid | 7 to 8 |
Food packaging | 8 | |
Vitamin and protein packaging | 7 to 8 | |
Electronics | Semiconductor | 5 |
Solar | 5 to 7 | |
Wafer fabrication | 5 | |
Medical Devices | Implantable devises | 5 to 7 |
Medical devise packaging | 7 to 8 | |
Medical devise reprocessing | 7 | |
Compounding | 7 |
EU GMP also give helpful examples of operations and grades for aseptic preparation and processing operations in cleanroom grades to help with specification.
EU GGMP grade | Application |
Grade A | Aseptic assembly of filling equipment |
Connections made under aseptic conditions (where sterilized product contact surfaces are exposed) that are post the final sterilizing filter. These connections should be sterilized by steam-in-place whenever feasible. | |
Aseptic compounding and mixing | |
Replenishment of sterile bulk product, containers and closures | |
Removal and cooling of unprotected (e.g. with no packaging) items from sterilizers | |
Staging and conveying of sterile primary packaging components | |
Aseptic filling, sealing of containers such as ampoules, vial closure, transfer of open or partially stoppered vials | |
Loading of a lyophilizer | |
Grade B | Background support for the Grade A zone (when not in an isolator) |
Transport, while protected from the surrounding environment, of equipment, components and ancillary items for introduction into the Grade A zone | |
Grade C | Preparation of solutions to be filtered including weighing |
Grade D | Cleaning of equipment |
Handling of components, equipment and accessories after washing | |
Assembly of cleaned components, equipment and accessories prior to sterilization | |
Assembly of closed and sterilized SUS using intrinsic aseptic connectors |
Specifying the size of your cleanroom
One of the main problems we see in cleanrooms is over population. All cleanrooms rely on air flow to keep the particulate levels within your specified classification. All objects within the cleanroom have an effect on this air flow and so it is important to have a cleanroom design that takes the equipment you will be using into consideration.
Selecting the position of your cleanroom
When selecting the position of the cleanroom a critical dimension to consider is the ceiling height. There are examples of where a cross flow or horizontal flow of air in more beneficial to a process but for the vast majority of cleanroom applications vertical airflow is the preference. This requires a certain amount of air filtration plant and/ or duct work to be positioned above the cleanroom ceiling height.
Temperature and humidity control to the cleanroom
Some applications require additional controls within the cleanroom. These can include static or ESD control, light and very commonly temperature and or humidity control. These requirements must form part of the initial cleanroom design brief.
When specifying temperature control the more information you can provide the more efficient the system will be both in terms of purchase cost and running costs. It may seem like a lot of questions initially but to get an accurate quote the information you will need at the start of the cleanroom design is as follows;
- the electrical loadings of every item that will be within the cleanroom
- the maximum number of people required in the cleanroom
- where the air handling plant can be positioned, inside or outside
- the temperature of the make up air. Will it be taken from inside or outside
- geographical location
Monitoring the cleanroom
With the update to Annex 1 more focus has been placed on monitoring. There are many ways to monitor a cleanroom dependant upon the class of the cleanroom, the required frequency of monitoring and the variables that you would like to monitor. We have great industry partners that can walk you through the design on this element to the cleanroom. Just mention it as part of your brief.
The above information will be enough information to get a quotation for a cleanroom.
Once complete you also have the option to add the new build validation package onto your cleanroom design which allows for testing and reporting at the 3 ISO stages. We also offer emergency cleanroom maintenance and servicing.
Cleanroom design and build specialists
We have designed cleanrooms on trains, in deserts, in the Antarctic and Arctic and underground. We love a challenge!
In order for us to quote for your cleanroom design we will need to know a little information to form your brief
Fill out the form on this page, or view our contact page for more methods of getting in touch with us