Cleanroom Validation
Cleanroom Validation
ISO Cleanroom are specialists in the testing and reporting of cleanrooms to the ISO 14644 series of classification. The report you will receive following your test meets the requirements of ISO 14644 and if requested EU GMP ensuring client facilities are audit ready and compliant with the requirements of regulatory bodies.
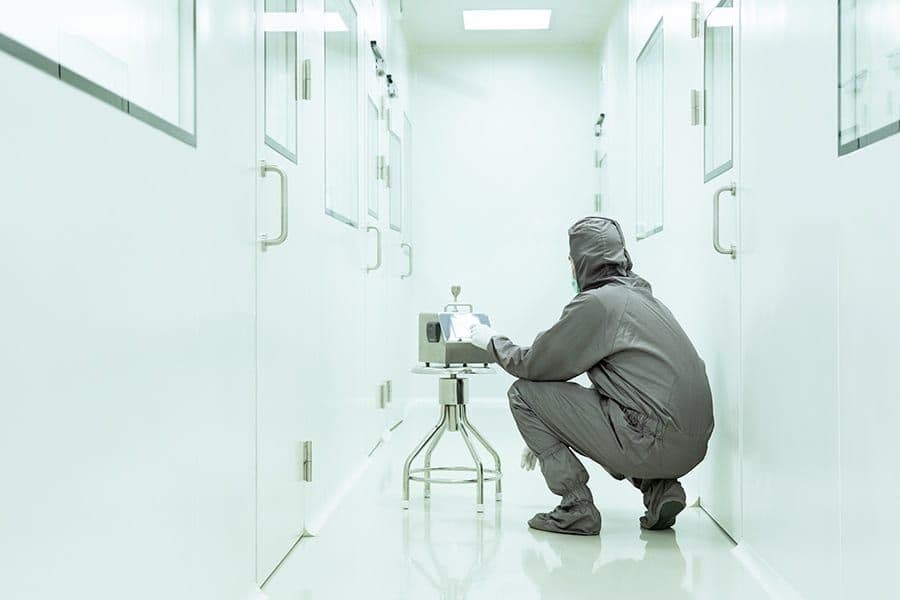
The ISO validation test can be performed in 3 distinct states;
- As-built. The bare bones of a cleanroom, an empty room not yet populated with any equipment and not in use.
- At-rest. The cleanroom has now been populated with any equipment required but is not in use, ie no moving parts and no personnel in the room during the test.
- Operational. The cleanroom is now fully operational and operating in accordance with the defined process.
Cleanroom testing and verification requirements
Cleanroom Qualification is the overall process of assessing the level of compliance of a cleanroom or piece of clean air equipment with its intended use. To meet the requirements for BS EN ISO 14644 Parts 1, 2, 3, 4 and 7 a cleanroom must be tested for:
- Airflow measurement – Volume and velocity.
- Airborne particle count.
- HEPA filter integrity test
EU GMP cleanroom testing
In addition to the above ISO requirements, if your process requires EU GMP qualification, Annex 1 asks for additional tests for the qualification of cleanrooms and clean air equipment (where relevant to the design/operation of the installation):
- Installed filter leakage and integrity testing.
- Air pressure difference measurement.
- Airflow direction and visualisation.
- Microbial airborne and surface contamination.
- Temperature measurement.
- Relative humidity measurement.
- Recovery testing.
- Containment leak testing.
ISO Cleanroom are able to offer all of the above apart from the microbial airborne and surface contamination tests.
The above tests are not exclusive to EU GMP cleanroom users of course. There are many circumstances where an ISO 14644 validated cleanroom would require additional testing.
We believe that the gold standard is not just to test for compliance but to monitor your cleanroom regularly through all three operational states to give a complete picture of the health of your cleanroom.
— TONI HORSFIELDCleanroom validation hints and tips
Your installer will test your cleanroom in an ‘As built’ state to prove the installation but you may want to consider a third-party validation.
Most cleanrooms are tested ‘at rest’ which is important data but the state that most customers are interested in of course is ‘in operation’.
Validation is not to be confused with the monitoring of the cleanroom which must take place at a regularity to suit your process. We are able to provide assistance in formulating your monitoring plan if required.
EU GMP calls for monitoring in 2 states; at rest and in operation as well as the time taken for the cleanroom to return to the at rest levels once the activity has finished.
Regular testing
Required test | Classification | Maximum time interval | Test procedure |
Particle count | ≤ ISO Class 5 | 6 months | ISO14644-1 2015 |
> ISO Class 5 | 12 months | ISO14644-1 2015 | |
Installed filter leak test | unidirectional airflow | 6 months | ISO14644-3 2019 |
and ≤ ISO Class 5 | ISO14644-3 2019 | ||
Non-unidirectional and > ISO Class 5 | 12 months | ISO14644-3 2019 | |
Airflow | unidirectional airflow | 6 months | ISO14644-3 2019 |
Non-unidirectional | 12 months | ISO14644-3 2019 |
Commissioning tests
These optional tests are recommended at commissioning then every 4 years and/or following significant changes to the cleanroom airflow or cleanroom activity
Required test | Classification | Maximum time interval | Test procedure |
Containment leak | All cleanrooms | ISO14644-3 2019 | |
Airflow visualization | All cleanrooms | ISO14644-3 2019 | |
Recovery time | All cleanrooms | ISO14644-3 2019 | |
Particle deposition | All cleanrooms | ISO14644-3 2019 | |
Segregation | All cleanrooms | ISO14644-3 2019 |
Suggested customer monitoring
Required test | Classification | Maximum time interval | Test procedure |
Air Pressure | All cleanrooms | Suggested daily monitoring | ISO14644-2 2015 |
Particle count | All cleanrooms | Suggested daily monitoring | ISO14644-2 2015 |
Environmental controls; temperature, humidity, light levels, ESD | If required suggest regual monitoring | ISO14644-2 2015 |
Taken from BS EN ISO 14644-2:2015. National annex. Guidance on maximum time intervals for periodic testing of cleanrooms and clean zones.
Particle counting test
ISO Cleanroom use a Light Scattering Air Particle Counter (LSAPC) with a flow rate of 50 LPM to measure your airborne particulate. Our particle counters measure from 03μm to 10μm and are calibrated yearly. The calibration certificate is included within your validation report.
Air Pressure test
It is necessary to show that the air flows in the correct direction between rooms in a suit of cleanrooms i.e. from clean to less-clean rooms. A pressure differential of 5 Pa,10Pa or 15Pa is required (depending on the design and number of rooms) with the cleanest area at the highest pressure. Your cleanroom may have pressure gauges installed but it is advised to check these instruments. ISO Cleanroom use a calibrated electric micromanometer to measure pressure differentials.
Air Flow testing
Air volume supply rates (m3/s) or air velocity rates (m/s) depending upon the design of your cleanroom will be measured using an array of instruments. Duct velocities will be measured by a static pitot tube. The average air velocity of filters is measured using calibrated vane anemometers or airflow measuring hoods (balometer).
Filter integrity test
Your HEPA and ULPA filters have been tested by the manufacturer, however it is necessary to ensure at installation that the filter has not been damaged in transit, during installation and that the installation has been successful with a good seal to the filter housing.
Damage can occur during the life of the filter if large particulate; perhaps released through maintenance operations hit the filter.
ISO Cleanroom have both a calibrated photometer and LSAPC and can conduct the test via either method depending on your processes sensitivity to outgassing.
Containment leek
This test is designed to detect intrusion of unfiltered air into the cleanroom from outside the cleanroom. Typical weak spots are wall joints, doors, ceilings and windows. These seals can of course degrade over time especially in spaces with large temperate variations.
ISO Cleanroom have both a calibrated photometer in combination with with the Laskin nozzle aerosol generator and LSAPC’s that can conduct this test. The choice of tests depends on your processes sensitivity to outgassing.
Recovery test
The recovery test is used to verify that the installation can return to a specified cleanliness level within a finite time, after being exposed briefly to a source of airborne particulate challenge. ISO Cleanroom would use either the Laskin generator to create a cold oil aerosol challenge or the microspheres, depending on your processes sensitivity to outgassing.
Airflow visualisation tests
The airflow visualisation test demonstrates the airflow direction and/or pattern which is compared to the design of the cleanroom or clean air equipment. This is shown using the Laskin generator to create a cold oil aerosol which can be photographed and filmed to evidence the flow. Or in cleanrooms sensitive to outgassing a taper or streamer can be used.