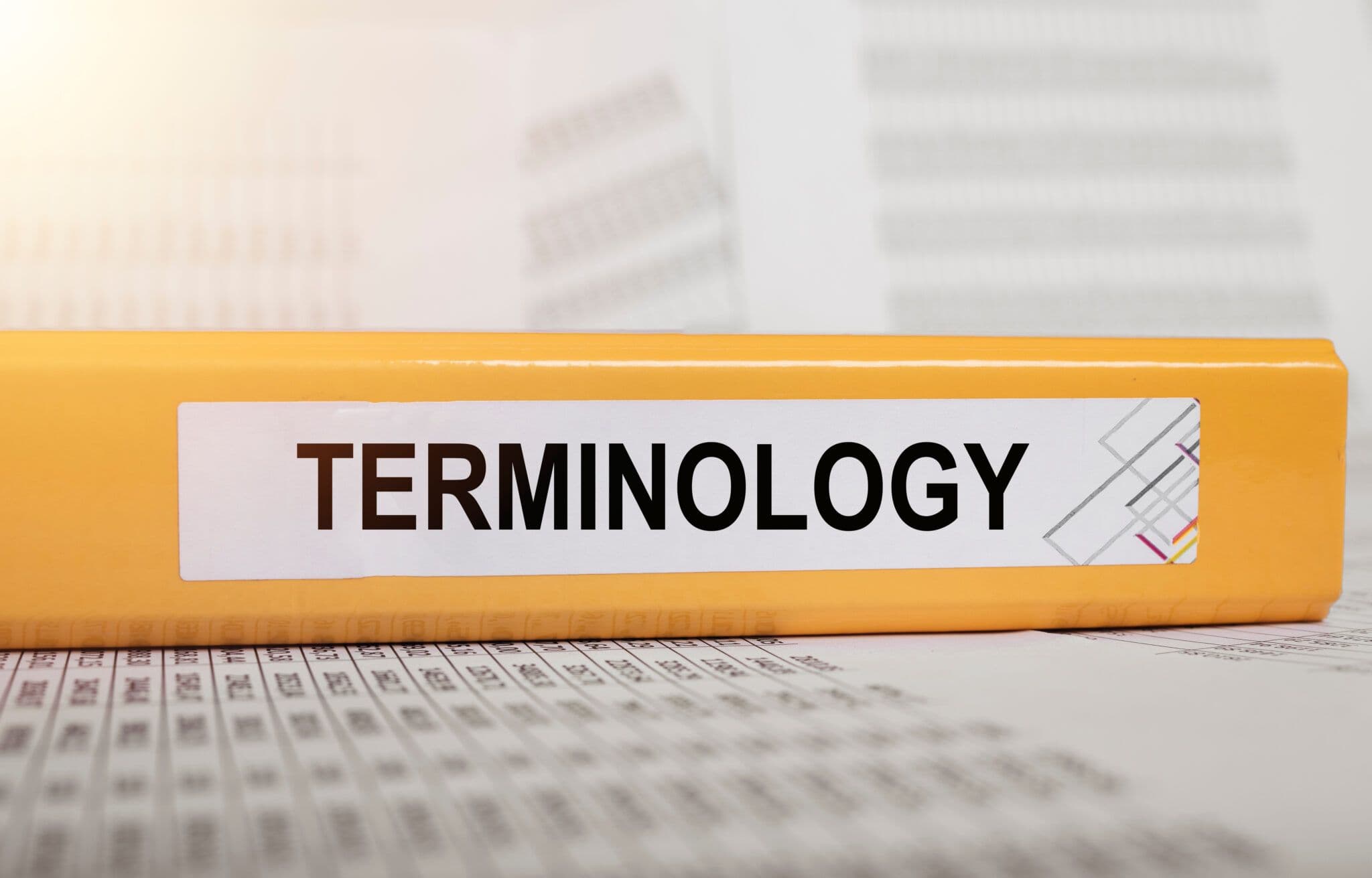
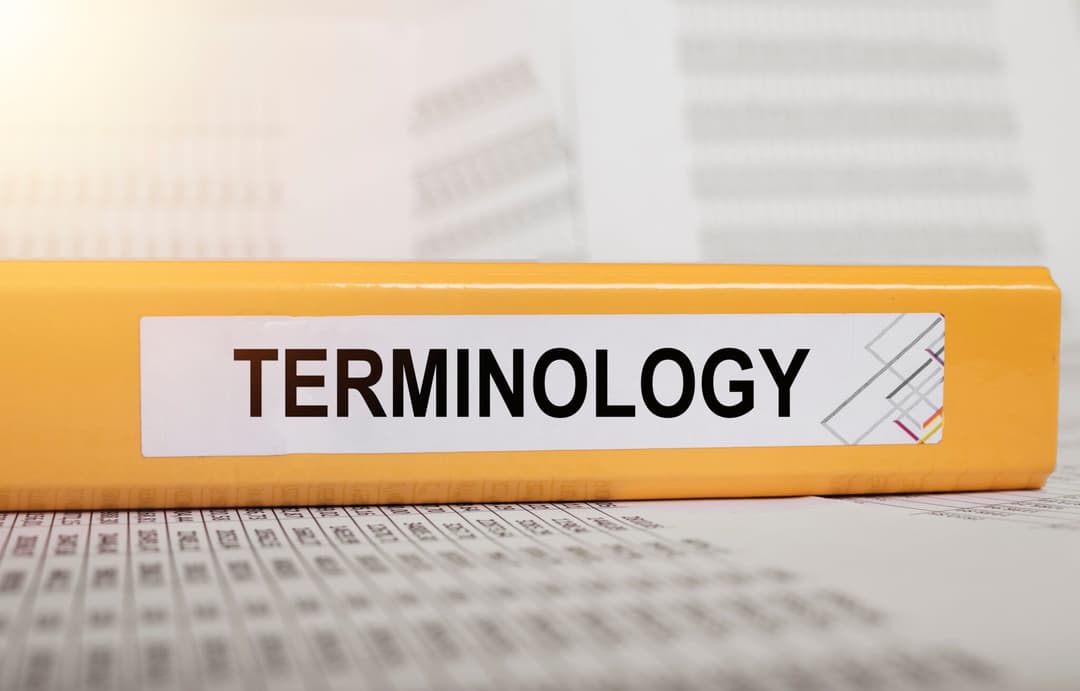
What’s in a name? Cleanroom terminology, what we say – what we mean – and how we bridge the gaps…
What’s in a name? Cleanroom terminology, what we say – what we mean – and how we bridge the gaps…
Cleanroom qualification, cleanroom testing, cleanroom certification, cleanroom commissioning, cleanroom verification and cleanroom validation are all words that are used regularly in our industry, but the important thing for us at ISO Cleanroom is understanding what our customers require – what they want us to achieve on their behalf – even if they are not using precisely accurate terminology for the service they need. But what do all of these terms actually mean…
Let’s start at the beginning:
President of the Contamination Control Network (CCN) Gordon Farquharson is a great authority on the requirements for taking a cleanroom concept to a working environment -and he has spoken widely about precise definitions.
In fact, he urges taking a step back, stressing that according to the GMP Annex 15, the route to an ISO 14644-1 compliant cleanroom begins with the specification – the User Requirement Specification (URS) to be precise: this is the foundation or starting point and is where the principles of Good Engineering Practice must be established, covering:
- Design and installation incorporating safety, health, environmental, ergonomic, operational, maintenance, recognised industry guidance, and statutory requirements.
- Professional and competent project management, engineering design, procurement, construction, installation, and commissioning.
- Creation and maintenance of appropriate documentation
Commissioning
Once the cleanroom has been designed and installed according to the Specification, ‘Commissioning’ is the stage where it becomes operational for the first time and includes working through any problems and solutions (getting rid of bugs in the system in every sense of the word!). All of these steps must be fully documented for interpretation by project engineers. In Gordon’s words, ‘Commissioning makes it right.’
Qualification
‘Qualification’ often happens in parallel with Commissioning and is about the documentation / evidence that ‘it is right,’ covering Design (DQ), Installation (IQ), Operation (OQ) and Performance (OQ) according to GMP quality impact (critical) features. A key aspect of Qualification Protocols is that they must be understandable by non-project personnel and external auditors.
Validation
Validation is about processes – the ‘how’ as well as the ‘what’. It incorporates the processes used to achieve Qualification, and good practice to ensure ongoing, continuous verification of all aspects of cleanroom maintenance, including computer systems, operational protocols and cleaning.
Where we come in…
ISO Cleanroom can offer independent testing in preparation for certification audits by our industry standards organisations:
For BS EN ISO 14644 Parts 1, 2, 3, 4 and 7:
- Airflow measurement – volume and velocity
- Airborne particle count
- HEPA filter integrity test (Installed filter leakage and integrity testing)
And in addition to these, if your process requires EU GMP qualification, Annex 1 asks for additional tests for cleanrooms and clean air equipment (where relevant to the design/operation of the installation): - Air pressure difference measurement
- Airflow direction and visualisation
- Microbial airborne and surface contamination
- Temperature measurement
- Relative humidity measurement
- Recovery testing
- Containment leak testing
ISO Cleanroom can offer all the above (apart from the microbial airborne and surface contamination tests) – and remember that many of these are not exclusive to EU GMP cleanroom users: there are many circumstances where an ISO 14644 certified cleanroom would require additional testing too.
As ISO Cleanroom founder and CCN board member.
We aim to be helpful, friendly and empathetic with our clients – listening to what they want to achieve, cutting through the jargon and communicating our knowledge clearly while providing quality services to enable them to reach their goals.
— Toni HorsfieldFor additional information about any of the other topics covered here, contact Toni at ISO Cleanroom, call 0161 529 2816 or email sales@isocleanroom.co.uk
You can also find our helpful guides on Cleanroom design at https://isocleanroom.co.uk/cleanroom-design/
Acknowledgements
Gordon Farquharson Gordon Farquharson | LinkedIn