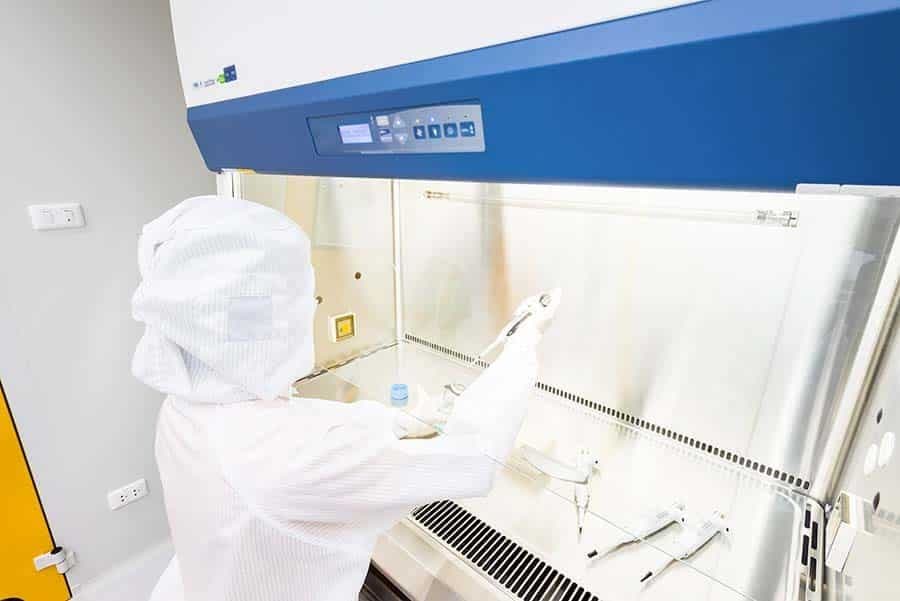
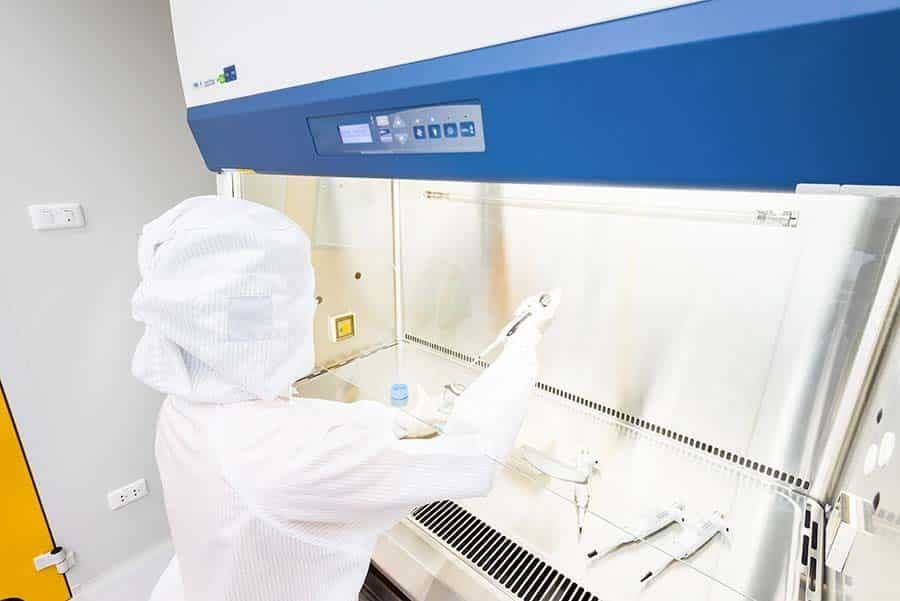
Cleanroom Cleaning Procedures
Cleanroom Cleaning Procedures
Personnel
This is usually the biggest culprit. Skin flakes, hair and droplets in the breath can easily contaminate the cleanroom without the proper PPE being worn.
Equipment
Any equipment entering the cleanroom or kept in the cleanroom must be thoroughly wiped down and checked regularly for rust, chips and any droplets eg oil.
Production material
Supplies could be brought in very regularly and so sources of contamination here might be dirty packaging, conveyor belts are particularly difficult to keep clean and so must be addressed in the cleaning SOP
Environment
This may sound like a strange one but if your cleanroom is in an industrial area and rubbish is being burnt you could find smoke particles in the cleanroom. If you are in a costal area salt maybe an issue, a dry area and you could find soil particles. These conditions should be identified at the briefing stage of any cleanroom design.
To cut down on contamination in the cleanroom there are a number of operating procedures you can bring into the cleanroom.
In a cleanroom of any ISO classification level it is important that all users walk slowly and avoid creating air turbulence.
Plan your day
To avoid too much movement and therefore turbulence in the cleanroom, gather all necessary materials, tools and supplies you will need to perform your job (such as cleaning solutions, wiping materials, assembly tools, testing tools and production forms, as well as actual process production materials).
Clean and inspect all incoming supplies, materials, equipment, tools, parts, carriers and carts (particularly the wheels). This involves looking for chipping, rusting and other signs of wear on metal tools and equipment.
All outside packaging must be cleaned or removed from the supplies or materials prior to taking them into the cleanroom. When possible, supplies, materials, equipment, tools, or product carriers should enter the cleanroom in poly bags or packaging.
Wipe down your work area at the end of each shift to allow time for the room air to settle down before the next work shift begins.
Know your air flow patterns at your work area and organize your work space accordingly.
Do not block HEPA filtered air from reaching the product with either your body or equipment.
Do not pin or tape notes or instructions sheets on walls or equipment that blocks the HEPA filtered air flow.
Keep tools, equipment and supplies in appropriate containers or designated areas until needed. Make sure they are down-stream of the product and will not contaminate it.
During lunch, or long interruptions in the work cycle, and at the close of the work shift, be sure that all products, supplies and materials are stored or covered to protect them from contamination.
Wipe up any spills immediately.
Re-clean any object that becomes contaminated.
Never touch exposed skin with gloved hand. If this happens change gloves.
Materials that shed particulate are not allowed in cleanrooms. These include;
- Cardboard,
- Paper,
- Wood,
- Natural fibres such as cotton, wool, rubber, leather
- Metallic surfaces such as furniture that has a coated or sprayed finish.
- Powder, spray and aerosol producing items. This can of course be very difficult if your product is a powder or spray. In these cases a fume hood should be used.