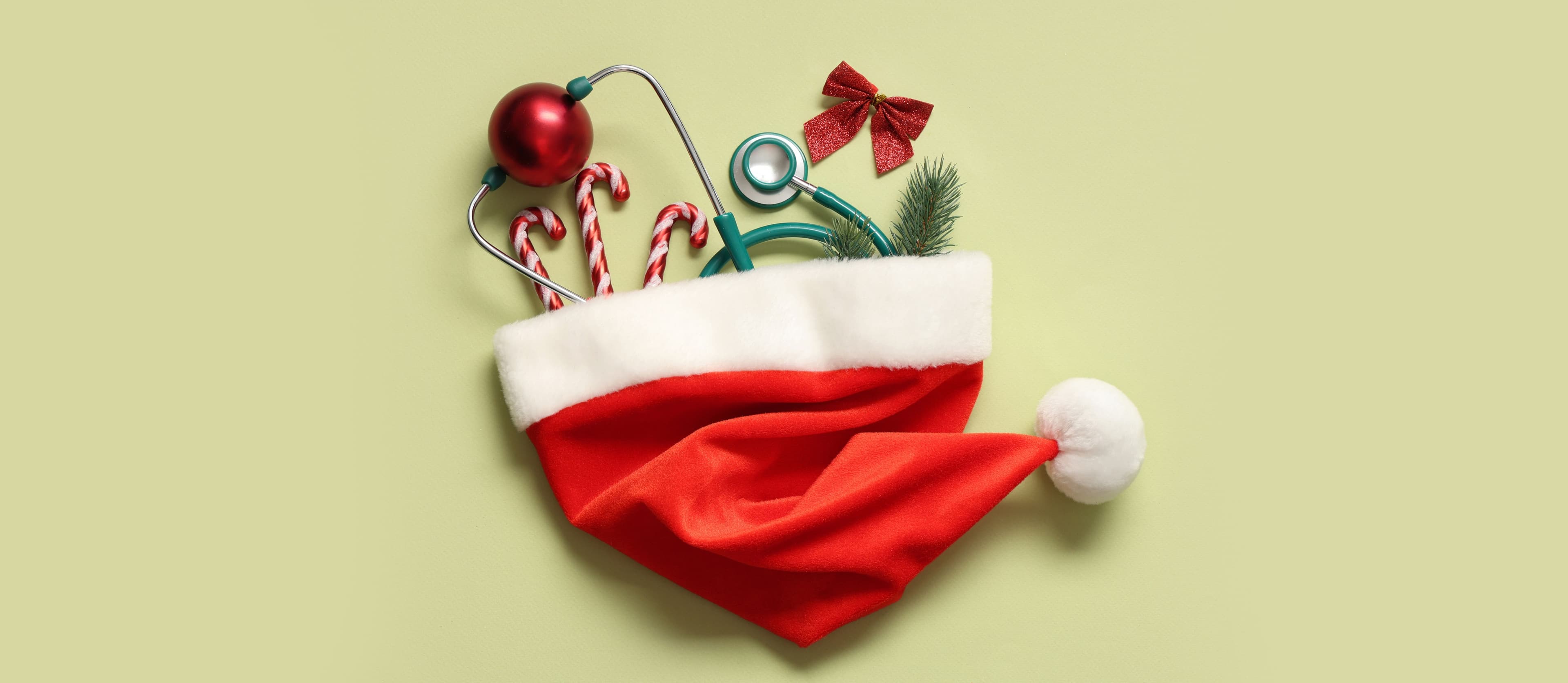
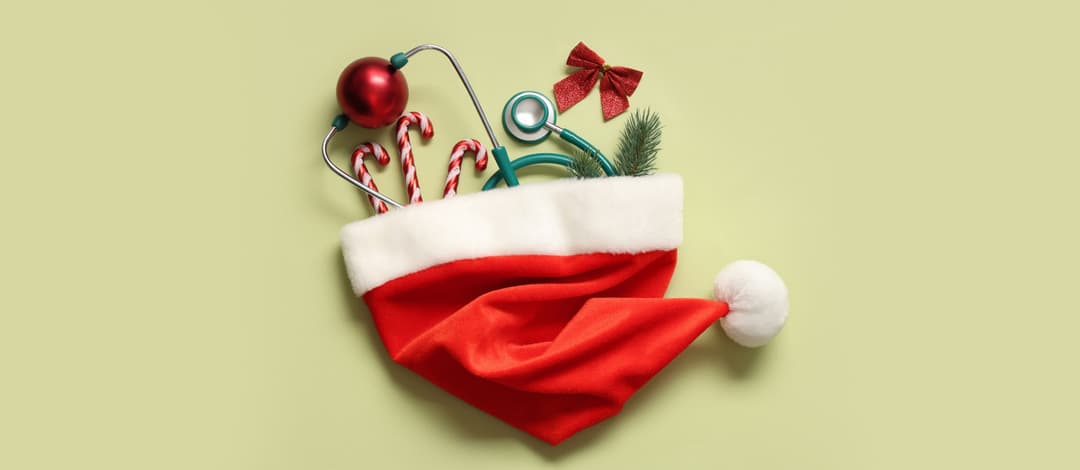
At a traditional time for storytelling: history of the cleanroom
At a traditional time for storytelling: history of the cleanroom
We’re not suggesting we can complete with those, but there’s another story that’s very close to our hearts – how the concept of cleanrooms came about, how they developed, and how they became an integral part of our daily life today.
Perhaps the earliest beginnings go back to the 1860s and a surgeon called Joseph Lister: at that time, even the simplest operation could have deadly consequences if infection set in, but he developed ‘antisepsis’ – or the use of antiseptic chemicals to guard against infection and make surgery safe. His system is still the foundation of infection control systems today.
He studied the ‘Germ Theory of Disease’ by French scientist Louis Pasteur and was the first to carry its principles into the operating theatre by introducing weak carbolic hand washes for surgical staff, carbolic acid baths for instruments and solutions of carbolic acid spray to reduce the level of germs in the air around the patient.
A royal connection
As with many innovations, there was scepticism at first, but over time, the number of surgery-related infections fell, and the practice of antisepsis became widely accepted by surgeons around the world. Lister even received Royal Approval when he used his carbolic spray during a surgical procedure on Queen Victoria.
https://www.sciencemuseum.org.uk/objects-and-stories/medicine/listers-antisepsis-system
Garments for contamination control emerged in the early 1900s and it was in May 1889 that the first pair of disposable rubber gloves was invented. It came about because a nurse complained that the carbolic acid and other disinfectants were causing a rash on her hands. The chief of surgery at Johns Hopkins Hospital in Baltimore, Maryland where she worked was Dr William Stewart Halstead, who contacted Goodyear Rubber Company to design the world’s first pair of disposable rubber gloves. His motivation may have been more than just being a great boss though, as the nurse, Caroline Hampton, later became Mrs Halstead!
(26) Rubber gloves and romance? It's not what you think! | LinkedIn
Back to the cleanroom…
So, although the idea of a contamination-controlled environment was already a concept to combat the risk of infection in the operating theatre, the impact it could have on manufacturing reliability and accuracy only became recognised during the second world war. That’s where HEPA filters were first used for the production of weapons and aircraft.
But the, man widely credited with the invention of an actual cleanroom using laminar air flow is American physicist Willis Whitfield, who was working with a team at the Sandia National Laboratories on nuclear technologies in the early 1960s.
The problem was that nuclear weapons components — mainly mechanical switching parts — were becoming smaller, and microscopic dust particles were preventing Sandia from achieving the quality the laboratories needed.
At the time, the practice was to seal cleanrooms tightly, direct all operatives to wear protective clothing and have a regular protocol for vacuuming. But this left a turbulent airflow which did not remove air particles.
Whitfield’s solution was to constantly flush out the room with highly filtered air which entered the room from a bank of filters that were 99.97% efficient in removing particles larger than 0.3 microns. For example, cigarette smoke blown in one side comes out the other as clean air, according to a 1962 Sandia Lab News article.
The air circulated in the room at a rate of 4,000 cubic feet or about 10 changes of air per minute, and a later modification, has the air passing down over the work area instead of across it, allowing gravity to help move particles into the floor, which was covered with grating. Filters underneath cleaned the air which was then circulated back into the room in a continuous cycle.
When the first cleanroom was tested, Whitfield said in a 1993 videotaped interview at Sandia:
The dust counters went to nearly zero. We thought they were broken!
What he had created was work environment more than 1,000 times cleaner than the cleanrooms in use at the time. And his achievement of what he described as a laminar (meaning constant, rather than fluctuating) flow is still the principle behind main unidirectional cleanroom systems today.
Whitfield eventually worked with NASA to provide planetary quarantines during missions to the moon and Mars and spacecraft sterilisation techniques, and the techniques were also being adopted by the medical industry, with Bataan Memorial Methodist Hospital in Albuquerque, which later became Lovelace Medical Center, being the first hospital to use laminar-flow cleanrooms in its operating rooms to prevent infections.
Charnley – our own UK pioneer
America may have been a leading light, but the UK also produced a cleanroom pioneer – John Charnley, a surgeon working in the North of England in the 1960s, who wanted to find a way to reduce infection in a particularly invasive surgery – that of joint replacements.
His concept was filtered air that was not only free of dust, but even more importantly, containing little or no bacteria. He achieved this by passing the air through an electric charge to remove the majority of the contaminated particles and the ‘cleaned air’ was then piped into a small operating theatre called the ‘Greenhouse’. Originally a temporary structure, Charnley later worked with Hugh Howorth, whose Bolton-based family business built and supplied air-filtration systems for the brewing industry. Together they developed a system that provided air that was 98% free of particles of two microns or larger.
Cleanrooms become the norm in industry
By the 1970s, the benefits of contamination control in manufacturing was widely recognised and cleanroom technology had become the norm for all kinds of industries.
This was formalised in 1976 with the publication by the British Standards Institution (BSI) of BS5295 Environmental Cleanliness in Enclosed Spaces. This was updated in 1989 – and again in 2004 when BS EN ISO 14644-5:2004 became the industry standard… and of course specific elements are changing all the time, such as the new ISO 29463-1:2024 global standard for HEPA and ULPA filters see our blog Going global: HEPA filters and a new standard - ISO Cleanroom
And finally…
So, nothing stands still and we are always looking for the next development, the next innovation that will take our industry on the next step of the journey: what will 2025 bring?
We don’t know, but from all the team at ISO Cleanroom, we wish you all the best at home and at work in the New Year!
So, nothing stands still and we are always looking for the next development, the next innovation that will take our industry on the next step of the journey: what will 2025 bring?
We don’t know, but from all the team at ISO Cleanroom, we wish you all the best at home and at work in the New Year!