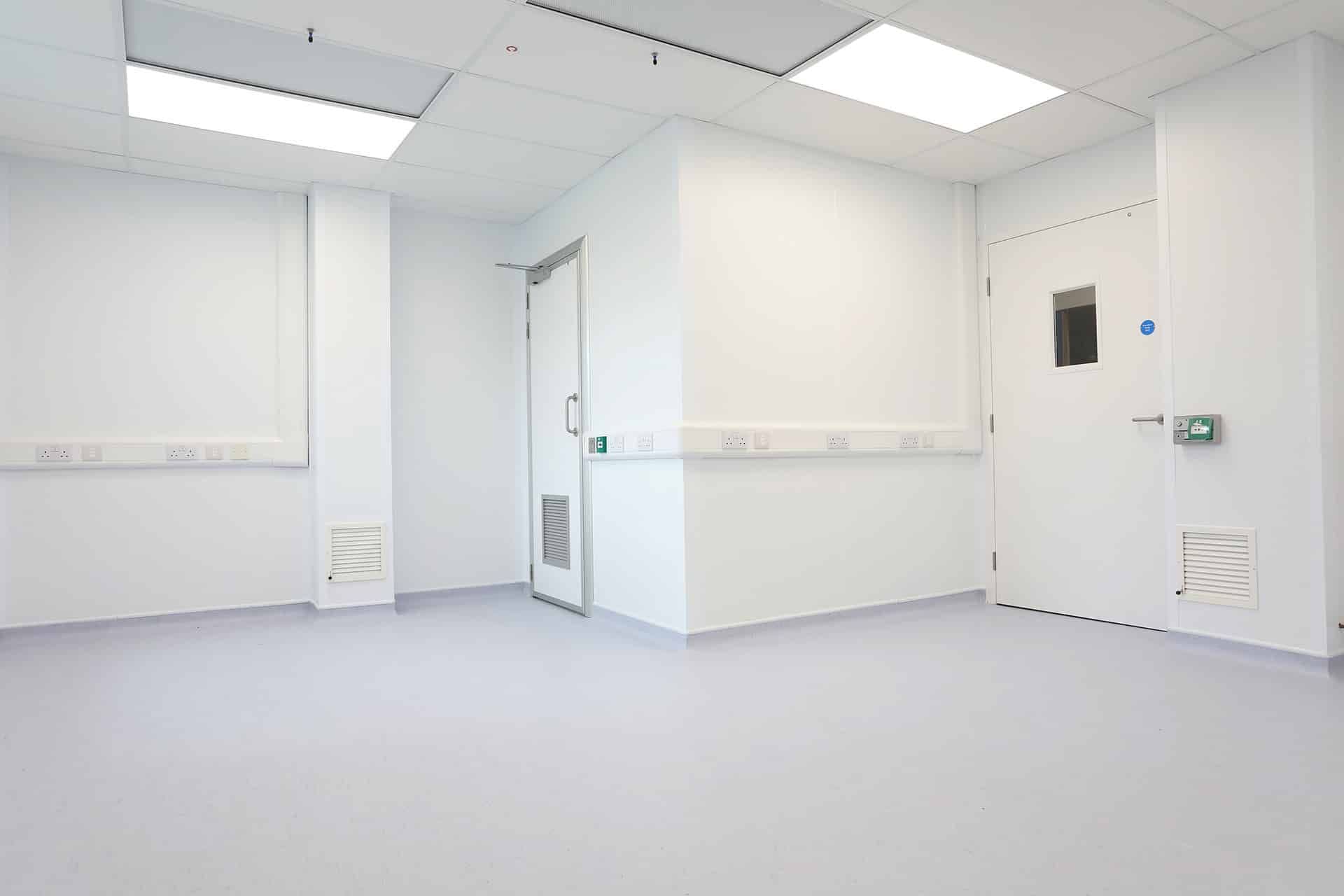
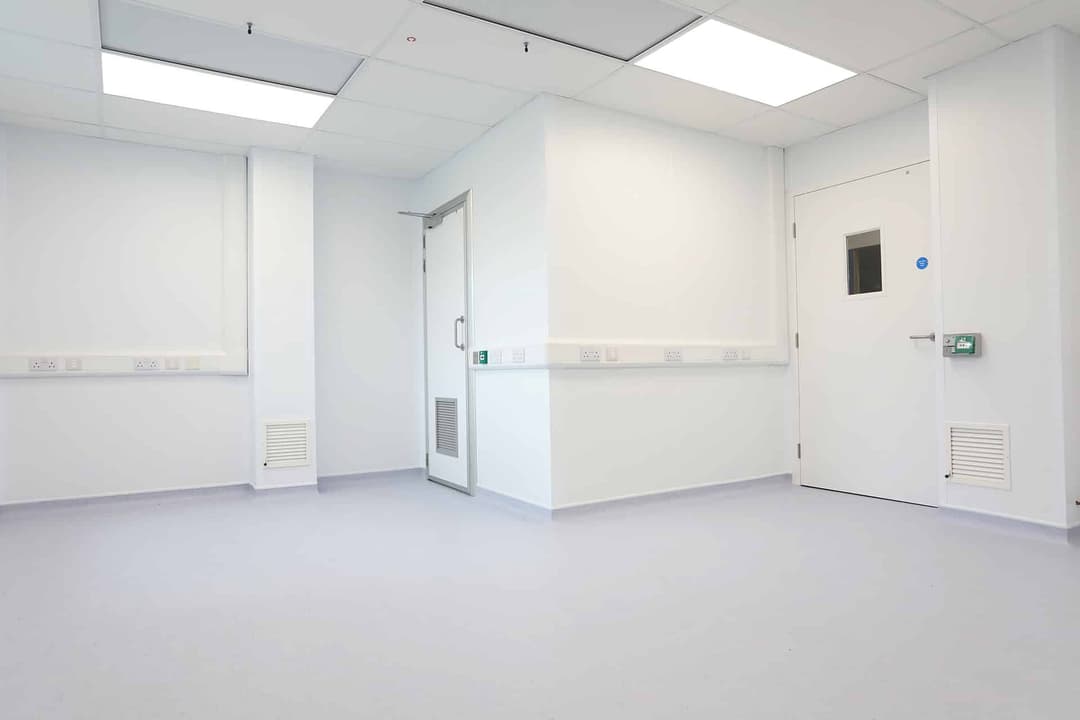
Cleanroom Build
Cleanroom Build
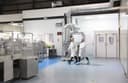
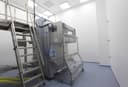
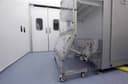
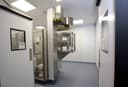
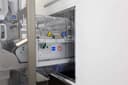
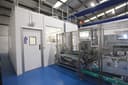
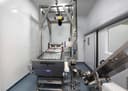
The cleanroom design process will identify all of the unique requirements in your cleanroom production facility and these will inform the exact construction method we use. There are many options available to us for all elements of the cleanroom build but the following details have been put together to give you a flavour of the materials we could use in your construction.
Cleanroom wall construction
Our standard cleanroom wall construction would typically use a PIR panel for the walls with a powder coated steel outer and a silicone seal. This gives you a very robust cleanroom wall and stands up well to a harsh cleaning routine. The thickness of each panel can vary from 50mm to 150mm depending on spans, fire ratings required, ceiling construction etc and will be detailed at the cleanroom design stage.
Cleanroom ceiling construction
The cleanroom ceiling construction will again be dictated by the design requirements but could either be a suspended grid ceiling or a walk on PIR panel or a combination of the two creating a plenum. The grid ceiling is set out to suit the terminal filters and lights allowing a degree of future flexibility. Additional flexibility can be designed in and has allowed our customers to easily segregate and upgrade the ISO level in sections of their cleanroom or to raise the ISO level or indeed lower the level of the cleanroom.
Cleanroom flooring
We have cleanroom flooring options for every cleanroom and sub floor construction but as a standard we would use a sheet vinyl, hot welded with a cove skirting. The advantage of a sheet vinyl is that it gives us the option of many additional features such as ESD control, antistatic, anti-microbial, different slip resistance options, chemical resistance options etc.
Cleanroom Budget Costing
A quick outline budget cost of your cleanroom design and build helps you to secure funding and so we like to firstly work with you to gather a budget cost based on a schematic cleanroom design. You may have a detailed brief, a full URS or are just at the start of your project but we will be able to put some assumptions together to give you a guide price.
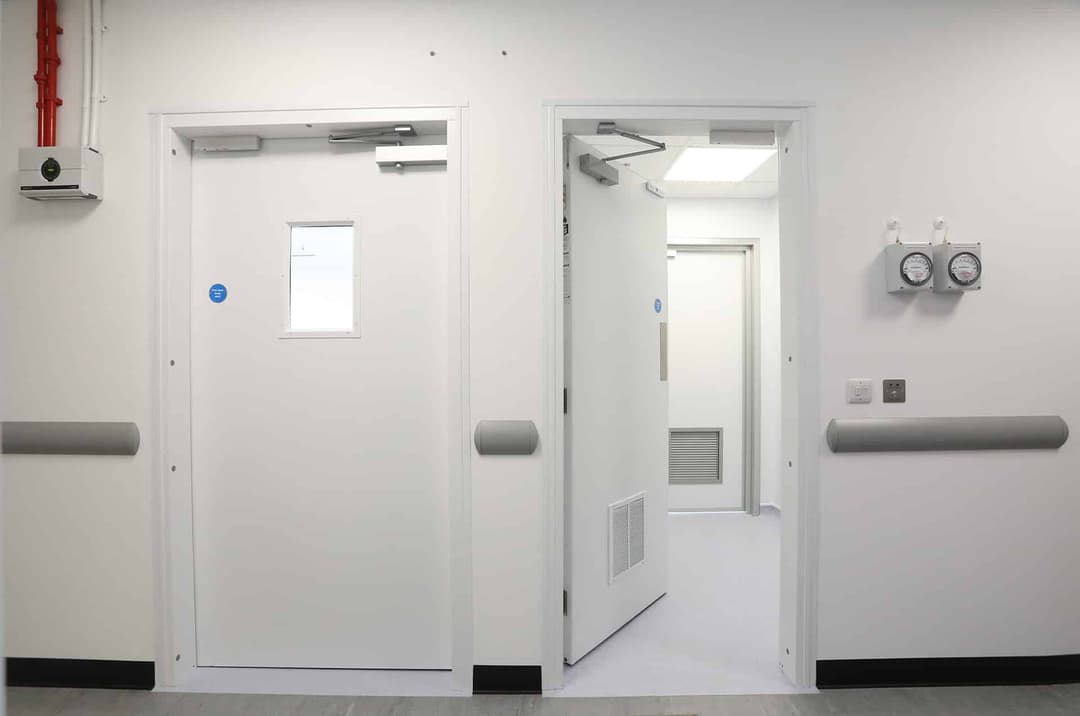
Our Approach to Cleanroom Build and Design
In addition to the briefing document or URS we will require some quite detailed information on the process to be carried out within the cleanroom.
The ISO 14644-4 design criteria changed in November 2022 and as such the design focuses on the rooms source strength or particulate burden as opposed to air change rates. In order for us to develop a design based on your specific source strength we will ask you questions such as;
- The maximum number of people you expect to be in the cleanroom at any one time (allowing for expansion)
- What the gowning protocol will be
- How you plan to move materials around the cleanroom
- What materials are likely to be in the room and to what quantity
- The machinery or equipment to be used in the room
- In addition to this information it may be beneficial for us to perform some testing of your process prior to a design to give us good data about the particulate levels we need to account for in our design calculations
Once a design has been agreed and signed by both yourselves and ISO Cleanroom we can then move to the manufacturing and installation.
The cleanroom manufacture will be lead by our projects director, Anthony Horsfield. Anthony is a building surveyor and commercial project manager with 28 years experience managing construction projects up to a value of £5 million. He is very hands on and has an eye for the detail required in production facilities. The build of your cleanroom facility is in safe hands.
Following completion of the cleanroom installation we will perform our ‘As Built’ or IQ (installation qualification) testing. The details of these tests will have been outlined in your quotation. The ‘As Built’ validation report forms the back bone of the sign off document and indicates that the room is now ready to be populated with your equipment. Once all the furniture and equipment has been installed the ‘At Rest’ or OQ (operational qualification) tests can be performed.