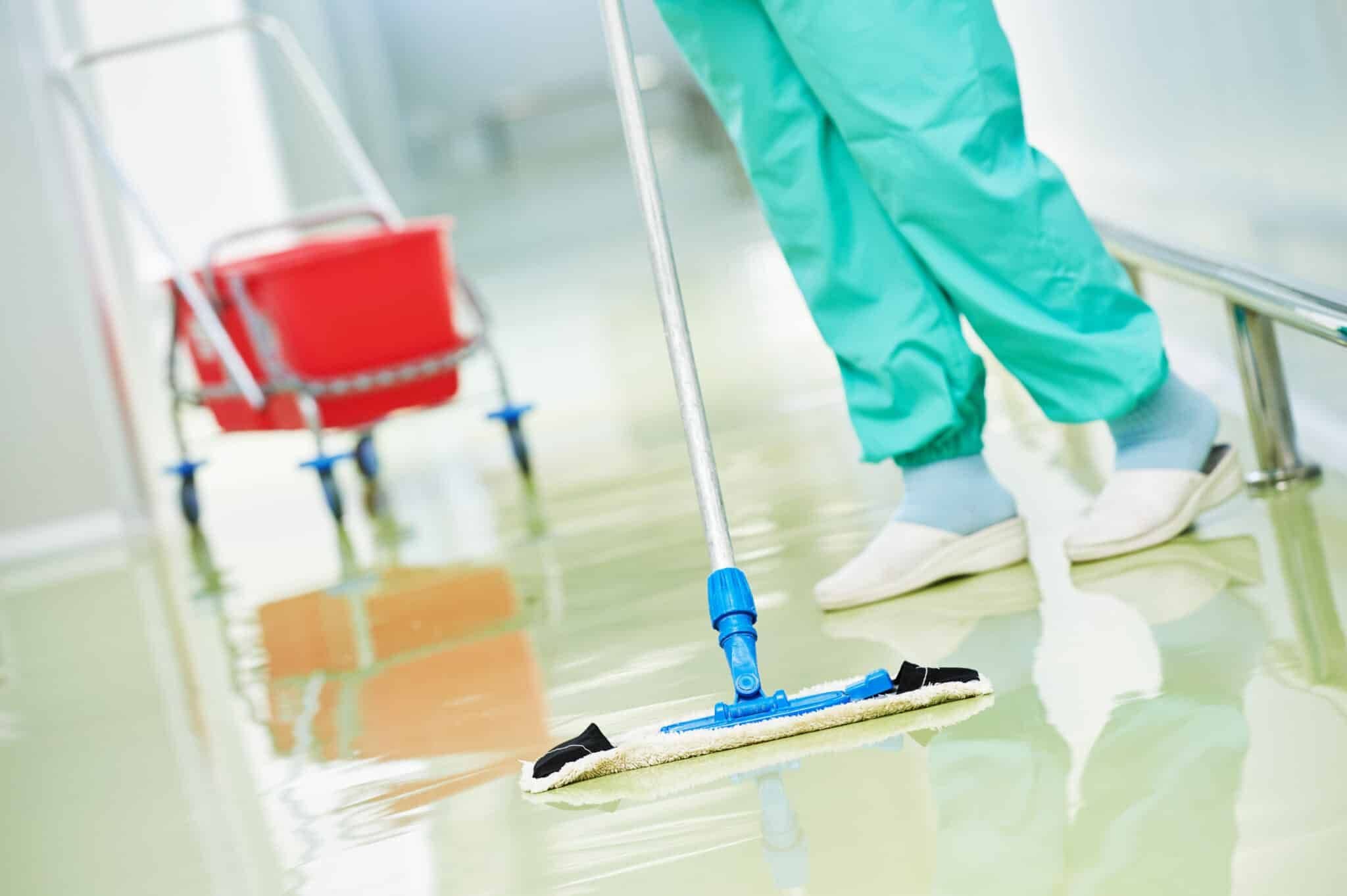
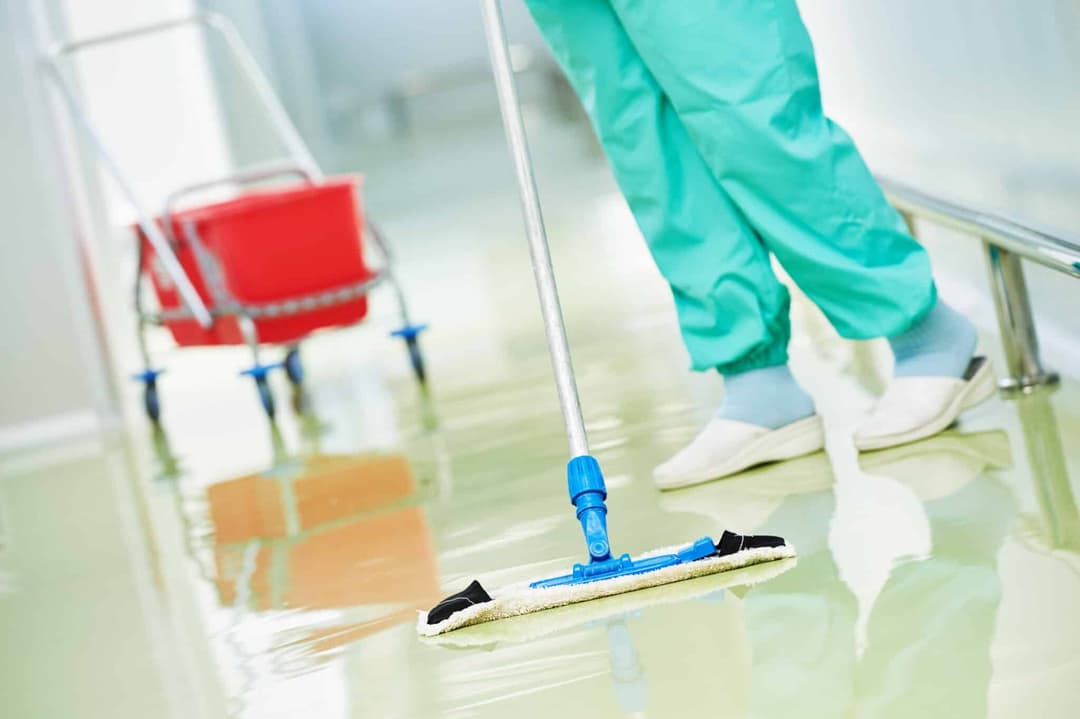
Critical Cleaning and Contamination Control – Best Practices for the Advanced Therapy Medicinal Products Industry
Critical Cleaning and Contamination Control – Best Practices for the Advanced Therapy Medicinal Products Industry
Add to that the usual risk factors including equipment, the facility itself and most significant of all, the personnel involved, and it’s clear that having rigorous and regular testing and cleaning is critical in this life science specialism.
At ISO Cleanroom we recently attended a presentation on the subject given by a senior technical service manager at STERIS Corporation, Jim Polarine, during the Cleanroom Technology Conference 2023 held in Birmingham.
It felt particularly relevant to us because we always stress the importance of rigorous cleaning protocols to all our clients. Here are some of the highlights from his lecture including useful insights and information on best practice:
Microorganism resistance hierarchy
An important aspect to take into account is the resistance of a wide variety of contaminants to different cleaning products including alcohols, disinfectants and sporicides. Factors including pH levels, temperature, contact time, concentration, surface construction, the presence of organic matter and water quality (although a necessary surfactant) can all impact effectiveness.
In short, achieving optimum contamination control is about finding the right balance between product efficacy, stability, compatibility, rinsing and safety /disposal.
Fungal spore outbreak
A case study, which dealt with an investigation into an outbreak of the fungal spore Aspergillus at a cell and gene therapy facility, revealed several early and visible warning signs (discoloured mop heads and tacky mats with a dirty appearance) as well as other issues:
- Inaccurate dilution rate of sporicide and disinfectants
- Incorrect cleaning and disinfection procedures for BSC hoods
- Use of excessive water for rinsing
Further investigation revealed additional areas of concern including:
- Materials (such as expired or ineffective chemical agents and damaged cleanroom surfaces)
- Measurement (including frequency of cleaning and disinfection)
- People (cleanroom behaviours, training and adherence to procedures)
- Methods (incorrect disinfectant concentration and application, inadequate sanitisation procedures for material transfer)
- Machinery (leakage in ceiling / HEPA filters, power outage and loss of pressure differential)
Key learning for maintaining cleanroom cleanliness
Among the conclusions were that validation studies of the disinfectant process (including product suitability and effectiveness) are a vital tool in managing cleanliness and should be carried out on a regular basis.
There is also a need for specific decontamination processes for equipment such as carts, which are brought into the aseptic processing areas from outside.
At ISO Cleanroom, as leading designers and builders of cleanrooms and we found Jim Polarine’s whole presentation very thought provoking.
I always say with a smile that Cleanrooms are not magic boxes. Regular cleaning with the right products is critical to maintaining your cleanliness level. The regularity, products used, and rotation of products will be determined by your risk assessment as informed by your settle plate and particle data. It is a key part of your SOPs. Most SOPs state that you must start at the cleanest surface (probably the ceiling) and work towards the dirtiest, usually the floor or bench top – and would usually advise to use a search pattern technique to wipe over each surface. As a general guide for your own cleaning routine, see our advice below.
— Toni HorsfieldISO CLEANROOM’s general cleaning routine guide:
- Use a 3 Bucket system (Bucket 1 – clean water, Bucket 2 – disinfectant, Bucket 3 – dirty water)
- Use a disinfectant as your daily clean with an occasional 70% IPA (alcohol spirit) clean to get rid of detergent residue
- Use a sporicide such as 6% hydrogen peroxide, probably once a month although frequency would depend on your settle plate data.
And frequency for specific areas:
Pre entry: suggest using a sporicide with a 70% IPA to remove residue left by your detergent to clean all items before they enter the cleanroom
Floors: daily for all ISO levels
Walls: daily for ISO 5; twice a week for ISO 6 and 7 and once a week for ISO 8
Ceilings: once a month for all ISO levels. Do not clean or touch HEPA filters as this would damage and possibly contaminate.
Drains: sporicide twice a month.
For more information and advice, contact the experts at ISO Cleanroom 0161 529 2816 sales@isocleanroom.co.uk or see isocleanroom.co.uk