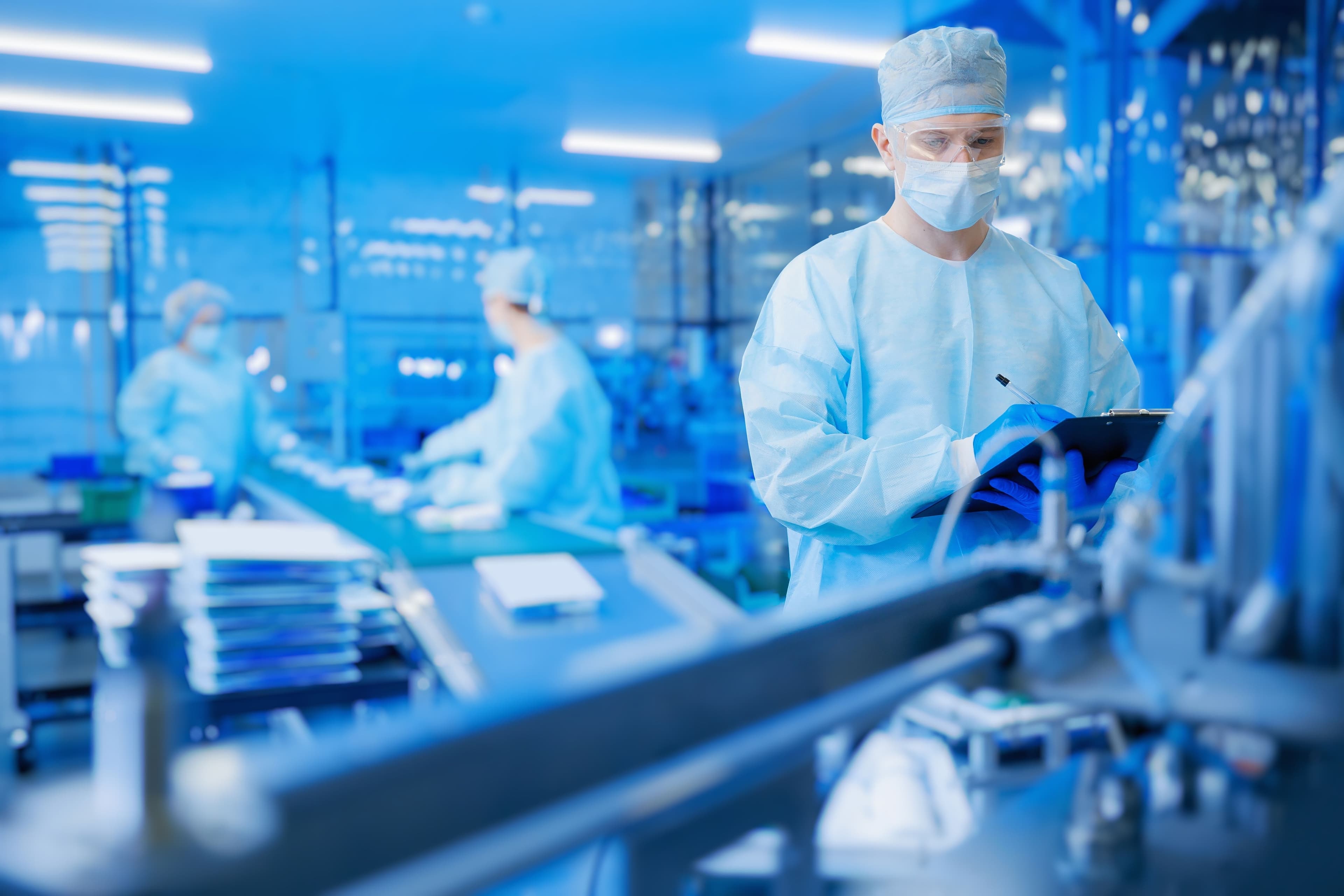
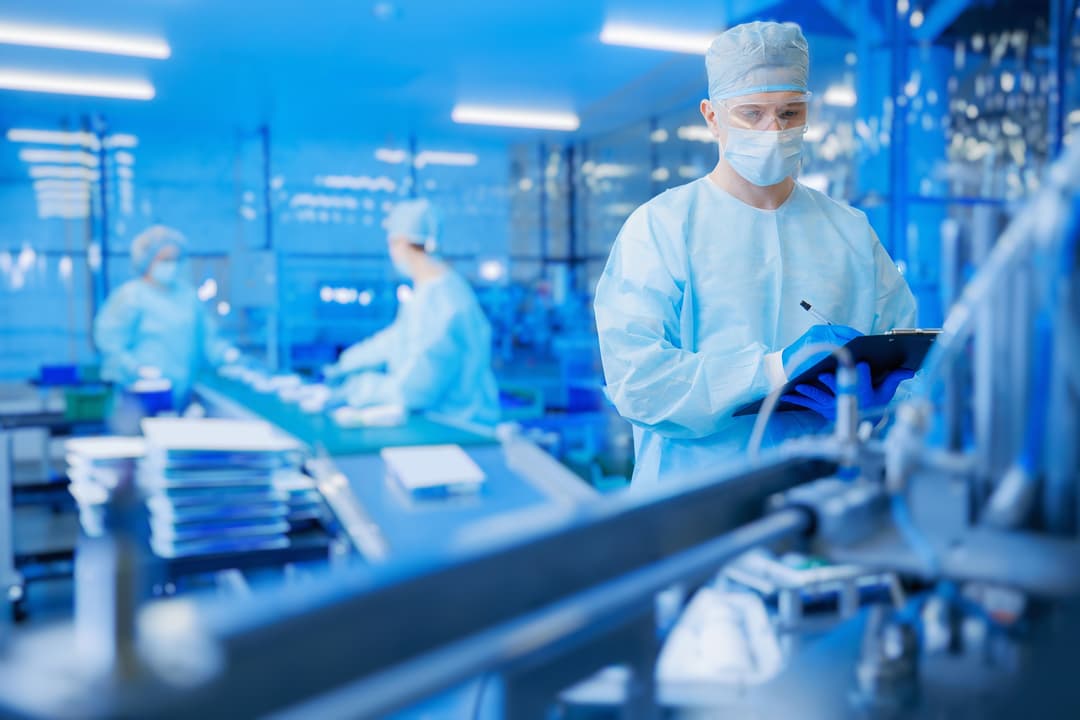
Clearing the air: explaining the confusions about particle counter configuration guidance in Annex 1:2022
Clearing the air: explaining the confusions about particle counter configuration guidance in Annex 1:2022
When Annex 1:2022 was published, instead of offering clarification, it originally created confusion among cleanroom operators.
Many of the concerns were specifically about guidance related to sampling airborne particles, particularly those ≥5.0 µm.
Industry Response
Recognising that something needed to be done, various bodies attempted to clarify the situation - in fact, the Swiss Medicines Inspectorate wrote a full paper to explain its intricacies and industry regulators finally responded by issuing Technical Report EN ISO TR 14644-21:2023, which has helped shed a little light… See https://www.swissmedic.ch/dam/swissmedic/en/dokumente/bewilligungen/inspektorat/-smi-ti-25e_interpretation_gmp-annex_1_2022.pdf.download.pdf/I-SMI.TI.25e_Interpretation_GMP_Annex1.pdf#
In a recent presentation, President of the Contamination Control Network (CCN) Gordon Farquharson also helped to set the record straight, specifically focusing on the areas of:
- People’s understanding of ‘classification’ versus ‘monitoring’.
- Correct adaptation of the ‘Macro particle’ descriptor taken from EN ISO 14644- 1:2015
- Sample tube length limitations
Classification and Monitoring
In essence, for classification it is the quality of the sample that is the most important factor, while for monitoring it is the quality of the data (discrimination of contamination deviation events).
Classification is all about establishing control and is covered in ISO 14644-1 Section 4.1.1, while the guidance for monitoring (which focuses on demonstrating control) is in ISO 14644-2 in section 4.1.2.
‘Macro particle’ descriptor
Another area where clean room operators were struggling with the new guidance was regarding procedures relating to larger particles.
In the new guidance, the ≥ 5 µm limits are no longer specified because inspectors found firms minimised qualification sample locations because these limits required very large sample sizes and long sampling times – over 30 minutes at each location, which was simply not practical. The emphasis is now on recommendations for minimising particle loss in sampling systems and ensuring accurate and representative data collection, which is essential for both classification and monitoring purposes.
Significance of sample tube lengths
All these points tie in with the issue of tube lengths, in which the guidance originally stated that manufacturer’s recommended specifications should be considered for tube diameter and bend radii, that tube length should typically be no longer than 1m unless justified and the number of bends should be minimised.
It went on to say that portable particle counters with a short length of sample tubing should be used for classification purposes, and isokinetic sampling heads should be used in unidirectional airflow systems and carefully positioned to ensure they obtain representative samples.
Some GMP regulators applied this guidance rigidly (e.g. 1m tube length) without recognising that 1m and short lengths can be difficult to work with in some equipment, such as filling machines.
The new guidance, for both classification and monitoring,now says that while, direct sampling without extended tubing is preferred, sample tubing is sometimes necessary for significant or critical locations: just keep it as short and straight as is practicable. The key is to evaluate the sampling system to assess the impact of any set-up compromises.
Summary
In essence, while ISO 14644-1:2015 sets the standard for cleanroom classification, ISO/TR 14644-21 provides practical guidance to address potential pitfalls in particle sampling, particularly for macro-particles, ensuring that users apply the standard correctly and effectively.
A key feature of the report is the inclusion of a decision tree (highly rated by Mr Farquharson who sees it as the most useful tool in the document), designed to help clean room operators identify appropriate sampling configurations and assess whether they need further evaluation. The report shows how this ‘decision tree’ can be used and includes practical examples of how challenges in implementing the guidance can be overcome.
With thanks to Gordon Farquarson for his recent presentation (which included additional material by Secretary of the CCN Stephen Ward, who is also Chairman BSI – LBI/30 Cleanroom Technology).
Other key references
- New Technical Report ISO/TR 14644-21 Explores Airborne Particle Sampling Techniques | Contamination Control Network (theccnetwork.org)
- ISO/TR 14644-21 (iest.org)
- Full published Document PD ISO/TR 14644-21 is available at the BSI Shop https://knowledge.bsigroup.com/products/cleanrooms-and-associated-controlled-environments-airborne-particle-sampling-techniques/standard