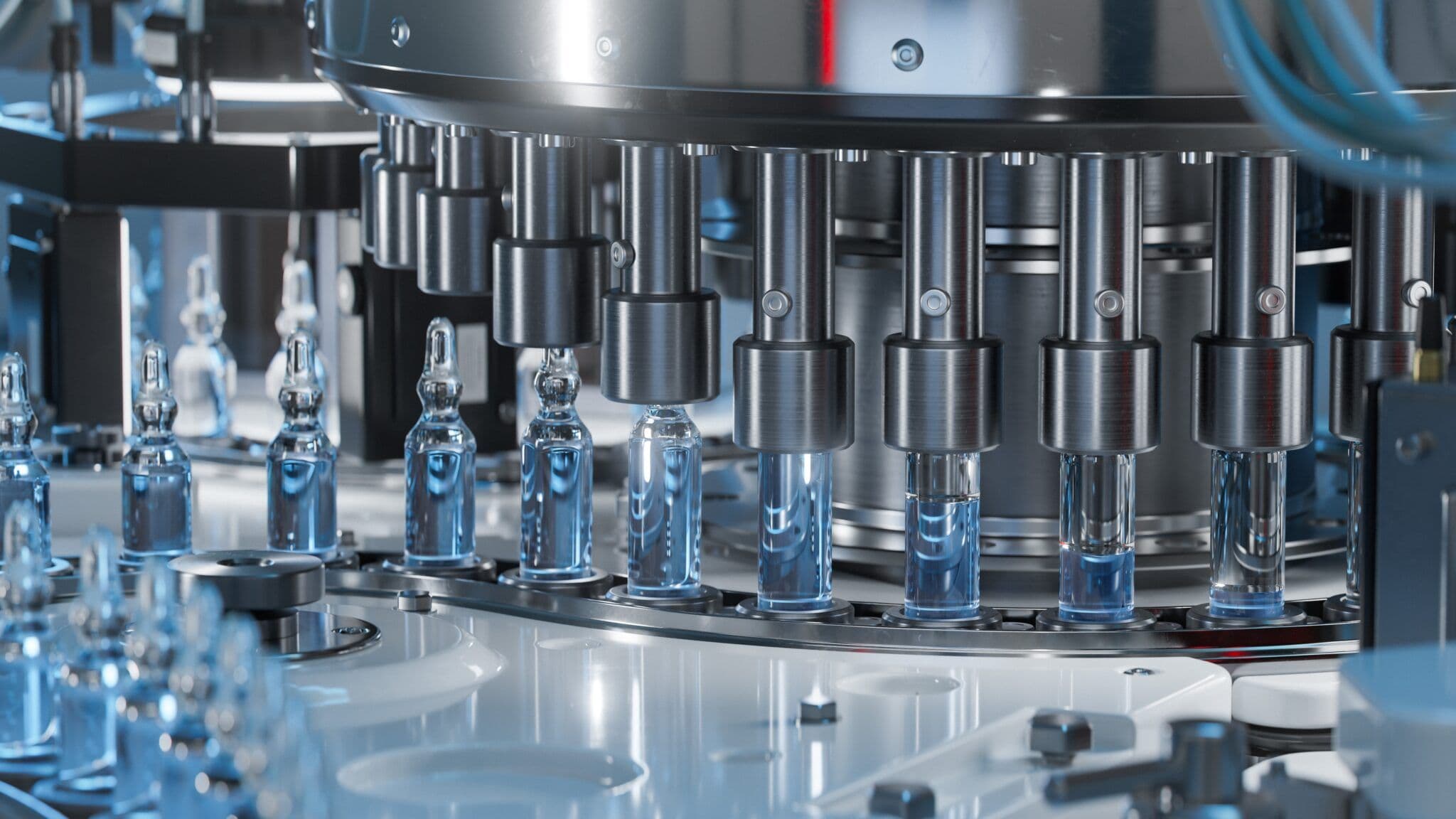
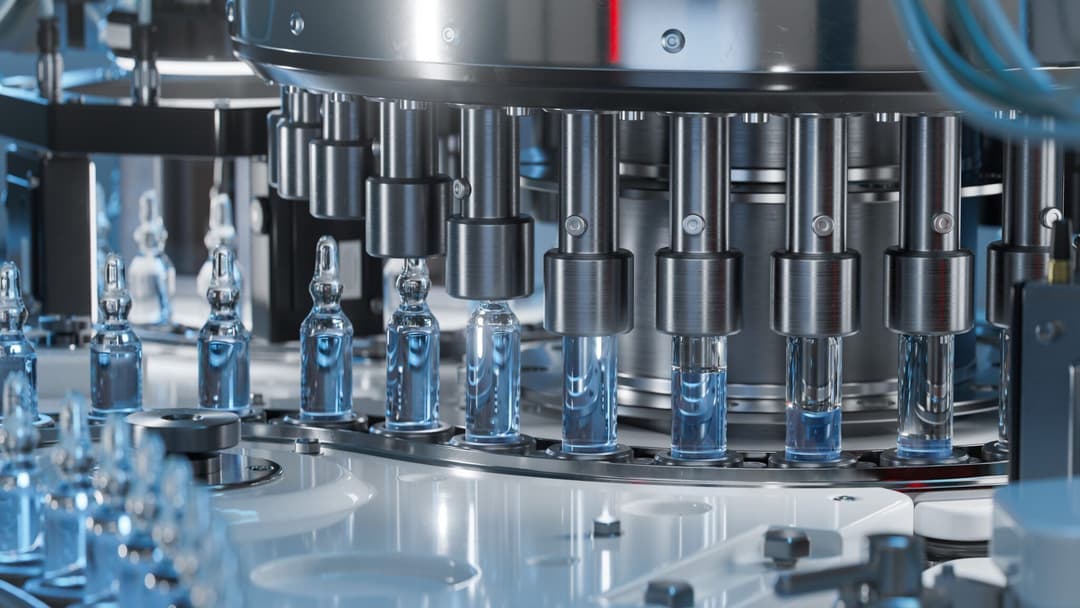
Cleanroom monitoring: what’s the right prescription in pharmaceutical production?
Cleanroom monitoring: what’s the right prescription in pharmaceutical production?
On 6th March 2024 Barry Cadden, a co-founder of NECC (a specialty compounding pharmacy) was sentenced to 10 to 15 years in Michigan for involuntary manslaughter after mould spores were found in steroid injections (mainly used for back pain) resulting in 100 deaths from Meningitis.
An extreme example perhaps, but the case illustrates just how important getting cleanroom monitoring right in pharmaceutical production can be: whatever formulation you are manufacturing (tablet, capsule, liquid, patch etc), contaminants can not only impact the efficacy of a drug needed for a life-threatening condition – they can harm or even kill a patient.
The recent updates to EU GMP Annex 1 lean heavily into the monitoring of contamination control environments within the pharmaceutical industry to give us the all-important warning if levels are approaching dangerous thresholds. But there is no ‘one size fits all’ blueprint as there are so many variables that manufacturers must contend with.
Starting with the right foundation
As ISO Cleanroom founder Toni Horsfield explains:
The first document that all manufacturing facilities will have created is the Validation Master Plan (VMP) as referenced in EU GMP Annex 1
This document walks through the full production process and includes the following additional documents;
- User requirement specification (URS)
- Design Qualification (DQ)
- Installation Qualification (IQ)
- Operational Qualification (OQ)
- Performance Qualification (PQ)
- Computerized Systems Validation (CSV)
- Process Validation (PV)
- Cleaning Validation (CV)
The VMP forms the backbone of the whole production operation and highlights all areas of risk, indicating the precise locations of how these will be monitored during the course of the process. In other words, it is during the compiling of this master document, along with the data collected from the cleanroom testing and validation reports, that the monitoring plan is formed.
It will ensure you measure all your production parameters including environmental conditions such as temperature, humidity, light etc. as well as particles, all of which may affect the outcome /quality of a drug, tablet, ointment etc.
For a recent ISO Cleanroom client who manufactures lozenges, moisture in the atmosphere was significant: sticky sugar won’t go through the machine unless the humidity is right!
Is it safe?
And there are all kinds of other potential hazards – our high school chemistry tells us that when certain chemicals get exposed to oxygen (or each other), they can have adverse reactions. Monitoring needs to ensure substances don’t have accidental contact, causing harmful changes in state during the process.
Some medications are incredibly time-sensitive – a chemo drug for cancer for example has to go from cleanroom to patient in a very short time period and so must be date and time stamped so that it can be checked before being administered.
At each and every stage, you have to be able to prove that you are achieving the relevant parameters to guarantee that when the drug arrives in the blister pack at your local chemist, shop or hospital pharmacy, it is safe to be administered to the patient.
Monitoring systems on the market
In the busy lab or cleanroom environment how do you make sure you are keeping within these safe parameters?
The answer is we must monitor all the variables and there are options in how you achieve this. A monitoring system can be as simple as regular particle counts with a handheld instrument and settle plates at positions identified in the monitoring plan, right up to fully integrated continuous automated monitoring systems, of which there a many on the market.
Full systems, such as those offered by ATI and PMT GB, provide particle contamination analysis in real time through continuous monitoring: alarms triggered when particle counts reach specified levels (below critical tolerances to make sure potential problems are identified early) and feedback for your team. They can include active microbial air samplers, sensors for temperature, humidity and light. Cameras of high risk areas. There are so many options and both companies have SMEs to help guide you to the system you need.
A note here, do not confuse the monitoring point plan with cleanroom testing and certification test points. In cleanroom testing ISO14644-1:2015 has a table of how many test points are required based on the area of the cleanroom and the room is simply divided into a grid. A monitoring point plan may have far less points, but they will be positioned at key risk points in the process.
— ToniYour key guide in choosing a monitoring system will be a Subject Matter Expert (SME), someone to help you understand the appropriate mix for what you are trying to do – the practicalities as your product progresses though the manufacturing process.
Portable real time microbial monitoring
A recent development which can aid real time monitoring is the introduction of Microbiological Monitoring Systems such as TSI’s BioTrak™.
These devices can split out viable particles from non-viables instantly. They are more accurate than settle plates or active sampling and give you a sample plate to incubate for species identification. As a new technology they are expensive but we see them as a very exciting development.
— Toni HorsfieldData: collecting and using it to inform your operation
All monitoring gives us a huge amount of data and simply collecting it is not enough… it needs to be read and referenced regularly to identify any small changes to trends before alarms are raised. This can be a simple spreadsheet or your system may include a bespoke database with interface which given the amount of real time data and historic data opens the doors to AI predictions.
Many such systems are currently in a state of development which will improve over time and that AI factor is likely to be increasingly important in spotting and predicting those vital trends in the future…
A word of caution on relying on system predictions. They can only interpret the data they are given and so in our opinion a human is required to sense check the information. The data may for example highlight problems which you can then trace back to internal factors such as shift patterns change – a new team whose members work slightly differently, or perhaps haven’t had all the necessary training. Or external factors – if your plant is on an industrial estate, could the processes of other operators on site be causing a stress on the system at a particular time of day?
There are so many areas where AI is coming in and is going to be great, but we’re not there yet. Systems may just give you a red light sometimes – and that’s when you need a human to look at the whole picture and figure out what’s going wrong. Data collection can’t look out of the window and see building work on your industrial park.
— Toni HorsfieldThere are lots of data collection systems on the market which can work with your monitoring equipment to create a bespoke system or you may find a full monitoring system that suits your process needs. Either way clear data presentation will hold invaluable information when a change or alarm is raised enabling quick identification and therefore a quick remedy to the issue.
When buying your monitoring system, more expensive doesn’t necessarily mean better – it’s about tailoring it to the complexity of your production process. We don’t offer such systems – but we have trusted consultants specialising in monitoring who we can put you in touch with to help you identify what you need. Our broad advice is to keep it as simple as possible, and that takes us right back to the importance of the VMP which details the whole process, and your SME, who will help you understand what is required and how to put it in place. ‘At the end of the day, it all comes back to you, the manufacturer: you know your product and what needs to be achieved, and ultimately it is you who, like Barry Cadden, is responsible and accountable if things go so tragically wrong.
— Toni Horsfield