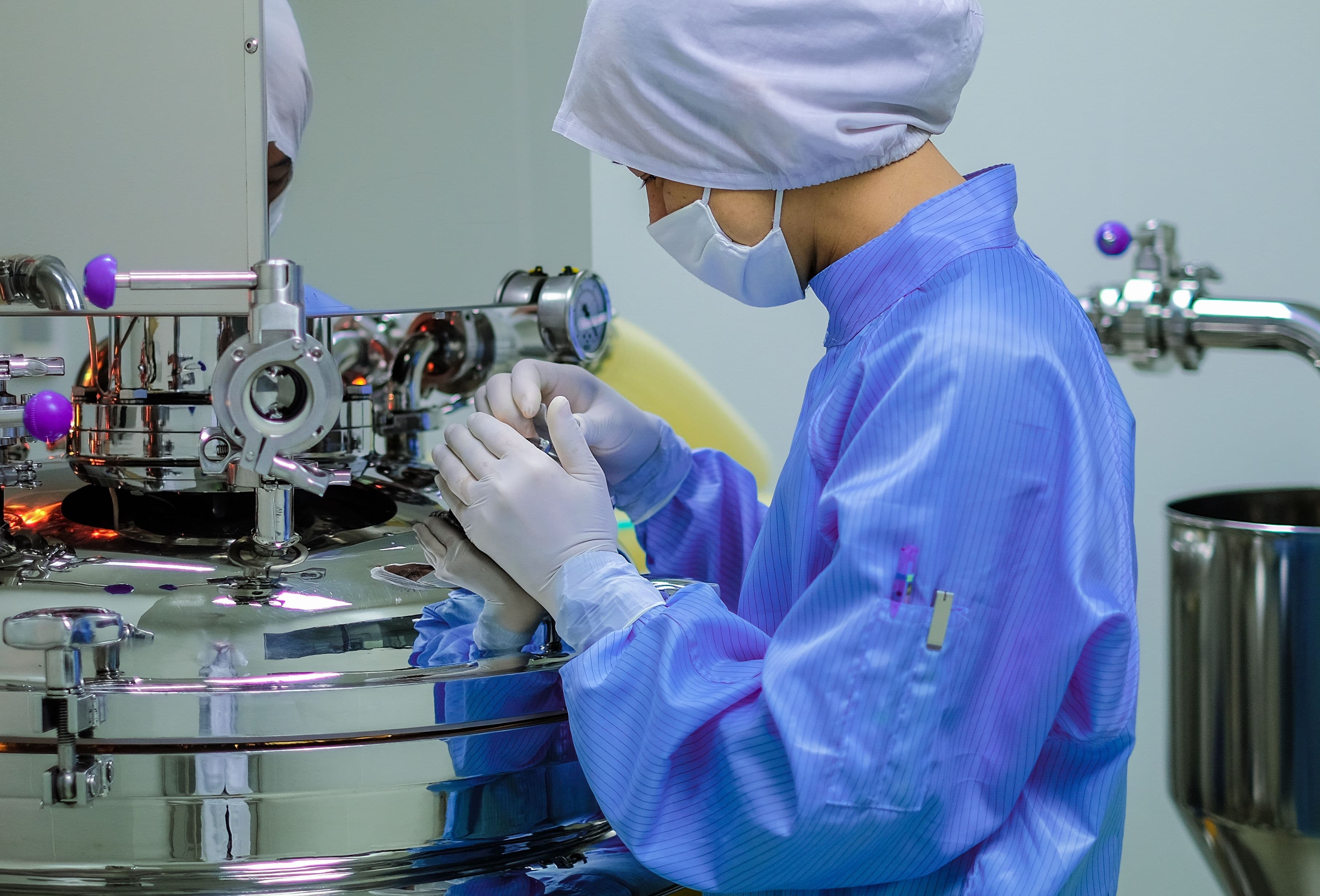
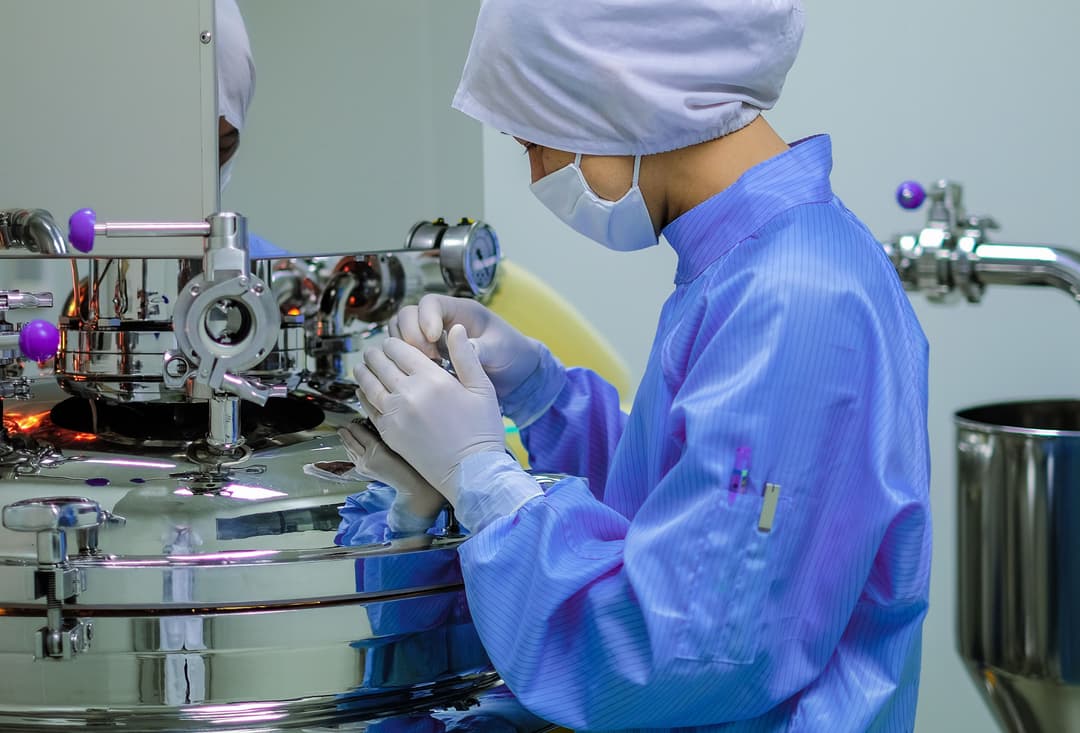
Cleanroom classifications: choosing the right standard for your process
Cleanroom classifications: choosing the right standard for your process
However, making sure you have the right level for your particular product or process requires careful consideration.
The aspects to take into account include legislation, safety, efficacy and cost: whatever you produce, you want to be sure it is compliant to any legislation, under safe environmental conditions, and working at peak performance. It might sound sensible to over specify the cleanroom to avoid any doubt but the higher the classification, the higher the costs associated with both installing the correct equipment, the energy usage driving up the running costs and your validation and testing regimes.
So there is no point in going for a higher classification than you need – you want exactly the right level for your process or product – and the right level might vary with different stages of your production process.
For example, in the case of high performance formular one cars, there could be advanced engineering components which need up to ISO 5 to ensure smooth running on race day when the difference between yourself and your competitor comes down to 0.008 seconds, while the exhaust system has a far greater ‘tolerance’ because of its operational requirements.
Hydraulics would be different again – anything from ISO 4 down to virtually no cleanroom protocol at all, depending on the product application.
In aerospace industries, most stages of the production cycle would need classifications between ISO 7 to ISO 5 – although processes such as isolation of injection moulded parts or manufacture of composite materials could require anything from ISO 5 to ISO 8.
Medical Devices and Pharmaceuticals are another area where the requirements can differ depending on the stage of the process – in the case of some implantable devices, the requirement is a stringent GMP grade A sterile environment which could be described as similar to ISO 5 – while for pharma packaging it is only ISO 8 or GMP grade D.
Broad brush: there is no ‘one size fits all’
The Classifications we’ve mentioned here are very broad brush. Within each production process there are nuances which require different environmental conditions. But if it’s not something you’re steeped in, you really need advice about what you need: you obviously want high enough for compliance, but don’t want to over spec and pay for something you don’t need because that affects the viability of your product.
— Toni Horsfield - ISO Cleanroom FounderIn some cases, classification requirements are clear either because the process is well used with plenty of industry data available or there is regulation stipulating the grade of the room required, this is often the case for those manufacturing pharmaceuticals under Good Manufacturing Processes (GMP).
In other cases, it’s about precedent and therefore customer expectations where orders will be lost if you don’t match the production standards in similar or competitor products. A cleanroom can also give you the competitive edge if you identify a failure rate that could be overcome with a controlled environment therefore giving your product the reliability.
It does get complicated because you have to keep drilling down, Every facet of an industry will have different requirements: ‘life science’ might be your industry overall, but a wearable device requirement will be different from a tablet, and intravenous drugs will have their own specific criteria. For our clients in these areas, where they have a good idea of what they need, we help them to refine their thinking, drawing on our extensive experience to ensure they come up with the most practical and cost-effective solution.
— Toni HorsfieldThe R&D perspective
An even greater challenge - and one the ISO Cleanroom team really relishes - is when a product or process is completely new:
‘Some of the entrepreneurs and inventors we work with are at the cutting edge of R&D: they don’t know what they need, because it’s never been done before. What we have to do is sift through to find the appropriate level for the environment they need for the product they want to produce.
‘Our expertise is all about asking the right questions and getting them to think in a particular way. It’s a question of identifying the vulnerabilities at the very core of key components - when they are likely to be the most exposed to outside influences - and working out how to minimise those risks.
‘If they are buying in elements such as chips etc. and their process is really just assembly, it’s very different from if the very centre - the nucleus of what they are doing - has to be exposed.
‘Through our discussions we will ascertain what size of dust particle could cause an issue together with the concentration that would have an impact. As a general rule if your product involves electronics, you will want to monitor those very small particles (up to 0.3 micron). However, if you are dealing with life sciences, food, or nutrients/supplements, concerns will be more about particles of 0.5micron and above to ensure you manage viable particles with sufficient mass that could develop into colony-forming particles.
Toni explains that they do engineer tests to help customers prove which ISO classification is correct for a particular process, particularly useful in an R&D scenario. ISO Cleanroom can provide an ISO Hood which is a small unidirectional hood (essentially a desk-mounted cleanroom – also called a clean or laminar flow cabinet) These ISO Hoods can take a range of filters and so the team can run tests with different filters to assess the failure rate.
A basis to work from
This will give us a solid base of information: essentially it’s a proof of concept for the system we finally develop: you need system X to limit the failure rate on your product to Y% – with Y being what you have chosen as acceptable. The key guides are within International Standard ISO 14644 Part 1 (2015) and its documentation includes a table (see below) which tells you how many particles at each different micron size are permitted for each level of the standard (usually the smaller the particle, the more you are allowed). Again, this is fine for someone who is well versed in this area – but when it is new, or people have only a top level understanding – that’s when we can really help. We have years of experience and understand not only the principles, but the nuances and fine detail that can be so important when looking at cost effectiveness, and the practicalities of building or testing a cleanroom facility that is fit for purpose for each of our client’s unique scenarios.
— Toni Horsfield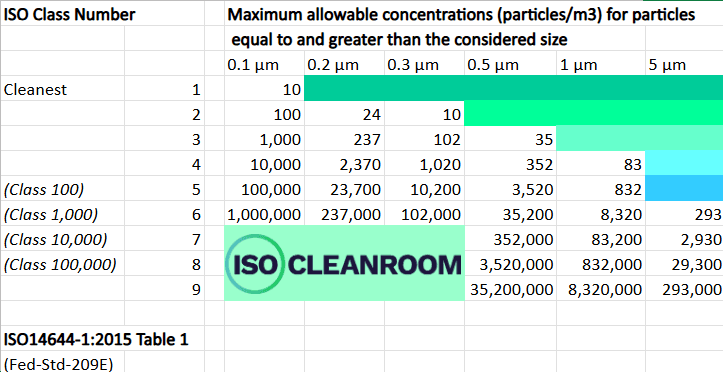
If you would like to learn more about Classifications, contact Toni at ISO Cleanroom, call 0161 529 2816 or email sales@isocleanroom.co.uk