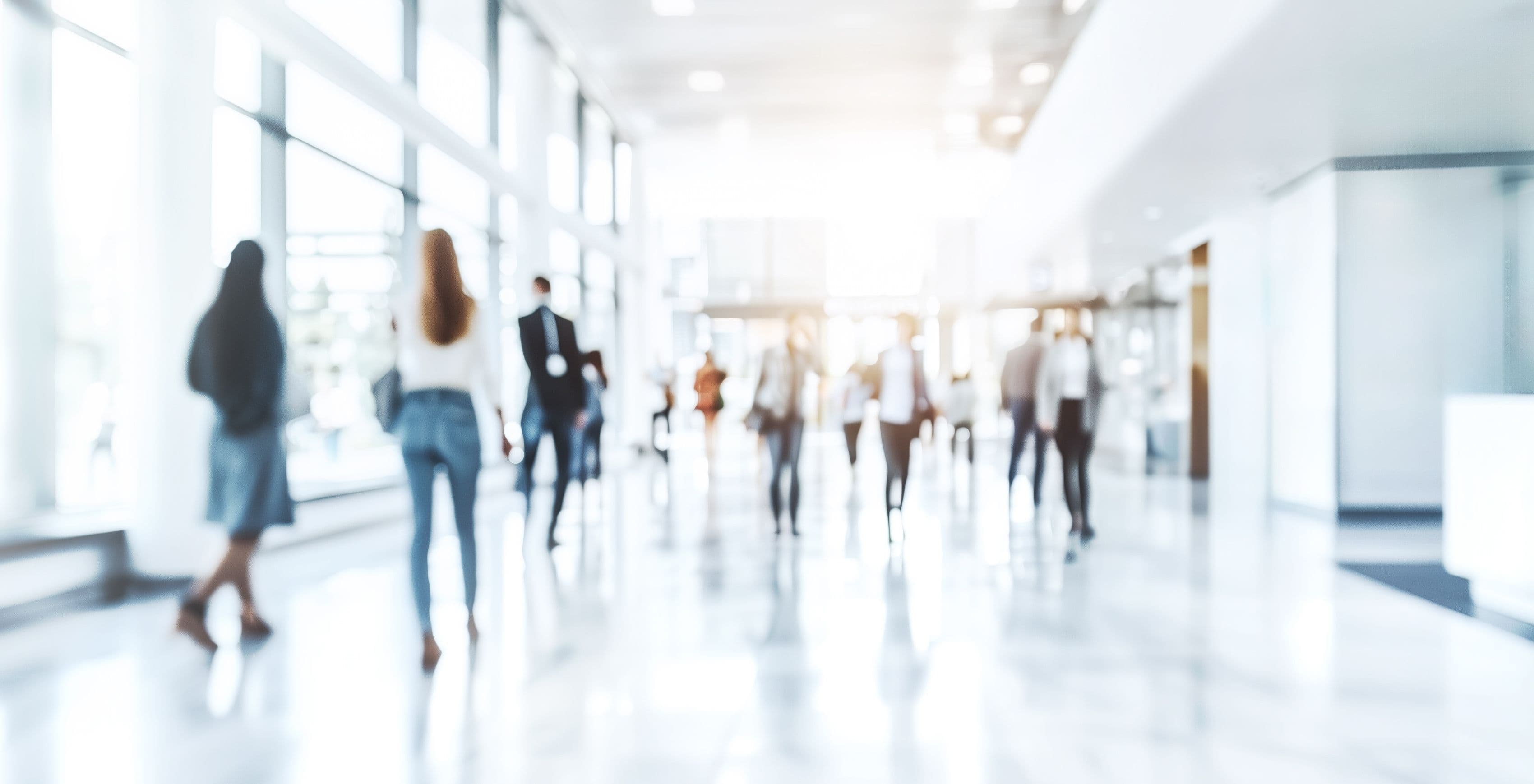
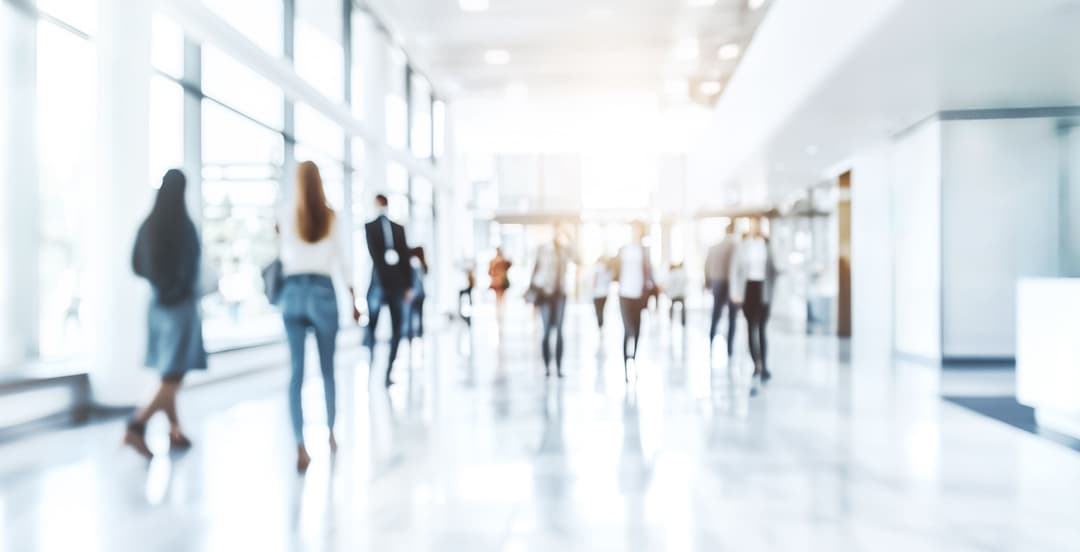
A day in the life of a Cleanroom Manager
A day in the life of a Cleanroom Manager
If you know anyone coming out of full-time education, who enjoys STEM subjects (Science, Technology, Engineering, and Mathematics) or has an interest in biosciences, a career in the cleanroom could be for them. Or it could be someone looking to take their working life in a new direction, who could take inspiration from a world which never stands still, buttouches so many aspects of 21st century living.
Today we have Wes Cherry:
Wes Cherry runs a cleanroom facility for a contract manufacturer producing critical testing components for medical diagnostics.
We supply components of testing equipment: essentially a precision measure of reagent in a reservoir which is used in analysis to screen patients for a specific issue. This might be a panel for a bacterial infection or a virus. There are many different applications for this technology – and more developments are coming out all the time. Our customers provide us with the raw materials - plastic chips with inbuilt wells into which we dispense reagent - and these are then returned to them as one component which they incorporate with other devices to create the finished piece.
He tells us about a typical day…
Our manufacturing operation runs 24/51/2 or perhaps we should say 24/6 – as shifts run slightly into the weekend – but essentially it is a Monday to Friday cycle, 6.00am-2.00pm, 2.00pm-10.00pm and 10.00pm- 6.00am.
There are two teams of three at each shift comprising a Shift Lead, Precision Dispensing Technician (Manufacturing Technician) and Support Operator. In my role as Cleanroom Manager, I operate ‘office hours’ unless I am covering for a Shift Lead – which happens quite often as I step in whenever anyone is on holiday or on sick leave. I enjoy doing this – it’s how I began my own career and means I see things first hand and stay close to the teams too. Each contract usually covers production indefinitely, but forecasts are provided between 3-6 months in the future – so we can plan some months in advance for exactly how we will operate for each contract.
In my ‘Cleanroom Manager’ role, my first job will be to speak with the Shift Leads to ask if everything is running smoothly – checking if they’ve had any problems to deal with, or indeed if there have been staff who have been performing particularly well.
Key aspects I will be reviewing are production volumes and quality, to ensure we will meet our contractual requirements. We build in an allowance for scrap rates, but we obviously want to keep these to a minimum, so they are a specific measure of our efficiency that I am constantly overseeing.
Essential to this is maintaining the sterile environment and ensuring there is no cross contamination and the key piece of equipment to achieve this is the ISO 5 cleanroom. The two teams can be working on different products (one each per day), so we divide the cleanroom in half and have completely separate sets of equipment (centrifuges, vortexes, water systems, curing ovens etc.) to use on each side – and there will be a full cleaning protocol of everything before we move to a different product.
The standards we work to are ISO 9001 (and of course GMP) – and we have also been preparing for audit to ISO 13485, which is the medical devices industry standard, as further evidence of how robust our manufacturing practices are.
All this means a lot of paperwork – which is also a big part of my day. While Shift Leads will complete their individual production logs, I will be signing them off for individual batch documentation (machine parameters / temperatures / timings etc.), and when you consider we can have around 30 runs a day – that’s 30 separate sets of paperwork! These records are really important – they’re all about adherence to specifications and having full traceability - and are key to providing the customer with Certificates of Conformity.
Checking and documenting our monitoring systems is another key task - there are equipment logs and cleanroom logs for things like cleaning protocols: surfaces are wiped down before and after each shift, and we have a deep clean once a week which includes hoovering / mopping of ceilings, walls, and floors.
Staff all wear full gowns and gloves (the principle is to keep exposed skin to a minimum), so we keep logs of these too – and I also have a training matrix to ensure everyone is up to date with standard procedures and any special extra requirements if a particular product or process demands it. Mostly it is about general things like changing gloves, and lifestyle aspects that could introduce particles into the atmosphere like the wearing of make-up or smoking (we ask people not to have a cigarette for at least half an hour before coming on shift).
We monitor the pressure in each part of the cleanroom: the gowning room, the materials room and the production area as we know this would potentially be our first sign of any problem with the mechanics of the cleanroom. We have a particle monitoring plan and take and record daily testing.
There are pre-filters outside the cleanroom and the air is then moved through HEPA filters before entering any of these cleanroom zones. Temperature is also an area that we monitor, but can’t completely control, but we have standing aircon units to help cool the cleanroom down during peak summer times. We inspect the pre-filters regularly, but this is part of what ISO Cleanroom do for us on their 6 monthly visits. Our cleanroom has always been tested and certified every six months through ISO Cleanroom.
As well as day to day management of these elements of cleanroom operation, my role includes customer liaison: we keep each client updated with current production progress through weekly meetings and can obviously respond to queries in between.
I will also be in regular communication with colleagues in the office: senior managers, the sales team and the logistics team for specifics like shipping (we ship daily) – labelling is key to this as it is vital that dates, sizes, weights etc are accurate for every batch.
Future work and planning and forecasting is all part of my role too – making sure we have schedules for customer projects as far as six months ahead.
And last but by no means least, it’s about people management – communicating with and supporting all my team members and ensuring they have what they need to perform to their best.
As you can see, I have set tasks, but because we have different clients and different products, there is still plenty of variety. It’sa great job – I’d thoroughly recommend it!